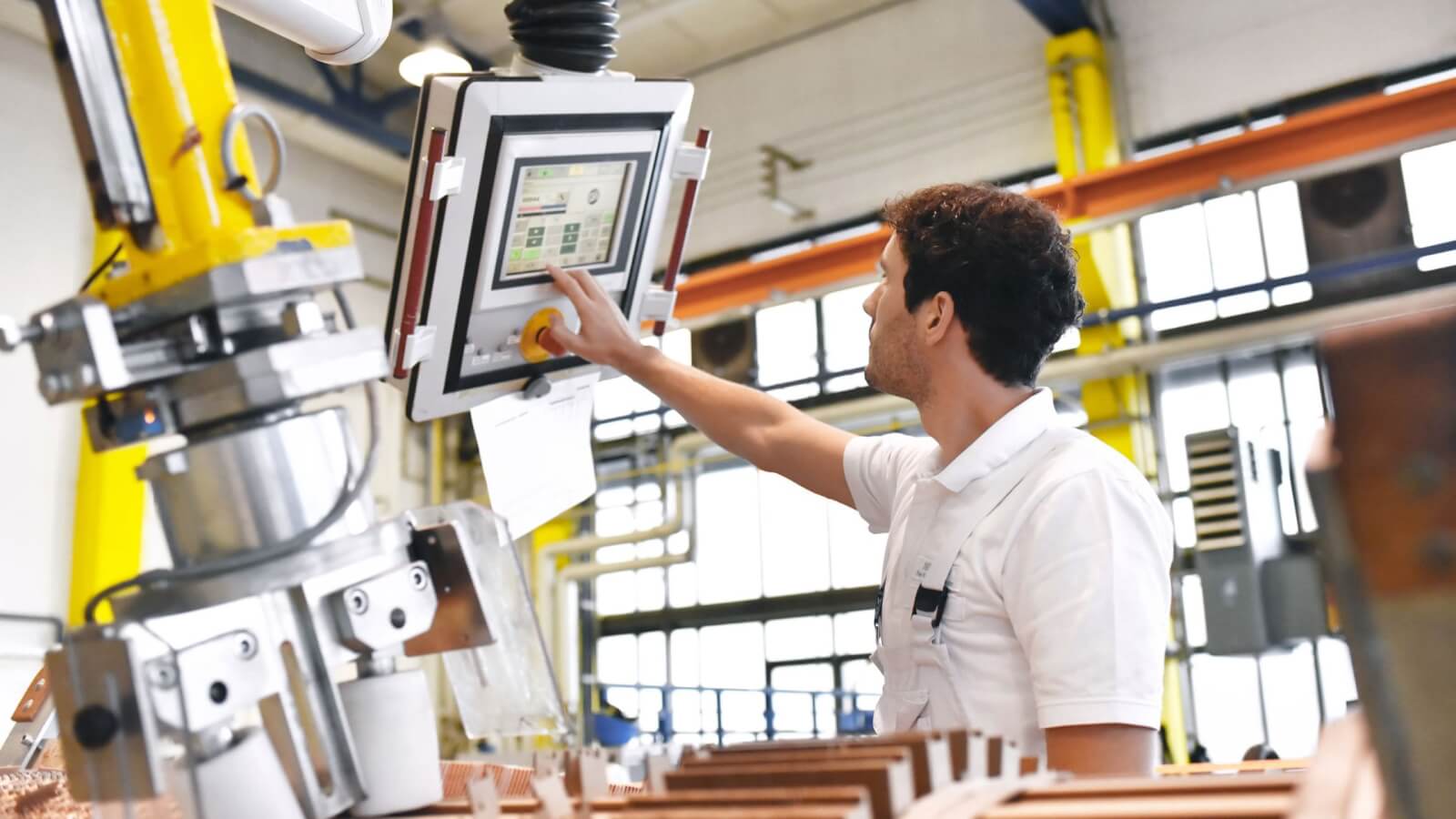
- In-process inspection ensures product quality and compliance during production by identifying defects early, reducing costs, and improving customer satisfaction.
- Key stages include raw material, post-assembly, and pre-packaging inspections, with methods ranging from visual and dimensional checks to functional testing.
- Future advancements, like AI, IoT, and predictive quality control, promise to enhance inspection accuracy, efficiency, and responsiveness to defects.
In-process inspection is a proactive manufacturing strategy that involves checking product quality at various stages of production. By identifying and addressing defects early, it reduces waste, enhances product integrity, and improves efficiency. Critical inspection points include raw material verification, dimensional accuracy during production, and pre-packaging quality checks. Techniques like visual, dimensional, and functional inspections utilize advanced tools such as high-resolution cameras, coordinate measuring machines (CMMs), and stress-testing equipment to ensure thorough assessments.
The benefits of in-process inspection include cost savings from reduced rework, improved compliance with standards like ISO 9001, and increased customer satisfaction through consistent product quality. However, challenges like resource allocation, maintaining inspection equipment, and adapting to evolving standards require robust planning and training.
Innovations like AI and IoT transform inspection processes by enabling real-time monitoring, predictive maintenance, and data-driven insights. These advancements and practices like statistical process control (SPC) and supplier monitoring support continuous improvement and help manufacturers maintain competitive quality standards across industries like automotive, electronics, and pharmaceuticals.
Leave a Reply
You must be logged in to post a comment.