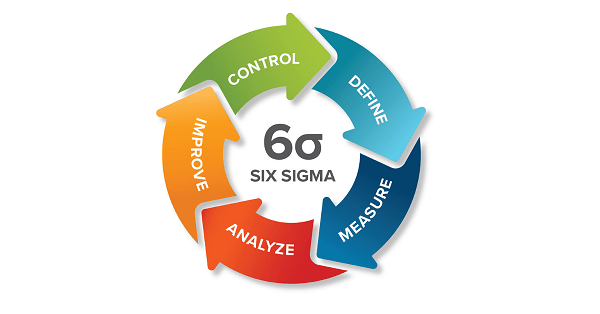
- Six Sigma’s data-driven approach, centered around the DMAIC framework, helps businesses optimize processes, reduce waste, and improve customer satisfaction.
- Implementing Six Sigma can enhance process efficiency, minimize defects, and drive significant financial savings across various industries by making informed, data-based decisions.
- Future trends in Six Sigma include leveraging big data, AI, and process mining, as well as a growing emphasis on real-time data and a data-driven culture.
Six Sigma is a powerful methodology that helps businesses optimize their processes by using a data-driven approach. At the core of Six Sigma is the DMAIC framework—Define, Measure, Analyze, Improve, and Control—which guides organizations through identifying inefficiencies, analyzing data, and implementing solutions. By relying on concrete data, businesses can avoid flying blind, making informed decisions that lead to improved efficiency, reduced waste, and happier customers.
Six Sigma has proven its value in various industries, from manufacturing to healthcare and finance. For instance, manufacturing companies use Six Sigma to streamline production lines and reduce defects, while healthcare providers apply it to enhance patient care and minimize errors. Financial institutions have also benefited from Six Sigma by reducing processing times and improving accuracy, leading to significant cost savings. Across all these applications, Six Sigma helps organizations focus on what is measurable and actionable, ensuring that improvements are meaningful and sustainable.
The future of Six Sigma looks promising with the integration of emerging technologies like big data analytics, artificial intelligence, and process mining. These tools enhance Six Sigma’s capability to handle complex data sets and automate processes, allowing businesses to gain deeper insights and achieve even greater optimization. Additionally, the growing emphasis on real-time data and the rise of “citizen data scientists” will further embed data-driven decision-making into organizational cultures, driving continuous improvement and long-term success.
By offering a structured, data-centric approach to process optimization, this staple of quality management can continue helping organizations across various industries significantly improve efficiency, quality, and customer satisfaction. By embracing this methodology and keeping pace with technological advancements, businesses can harness the power of data to achieve sustainable growth and success.
Leave a Reply
You must be logged in to post a comment.