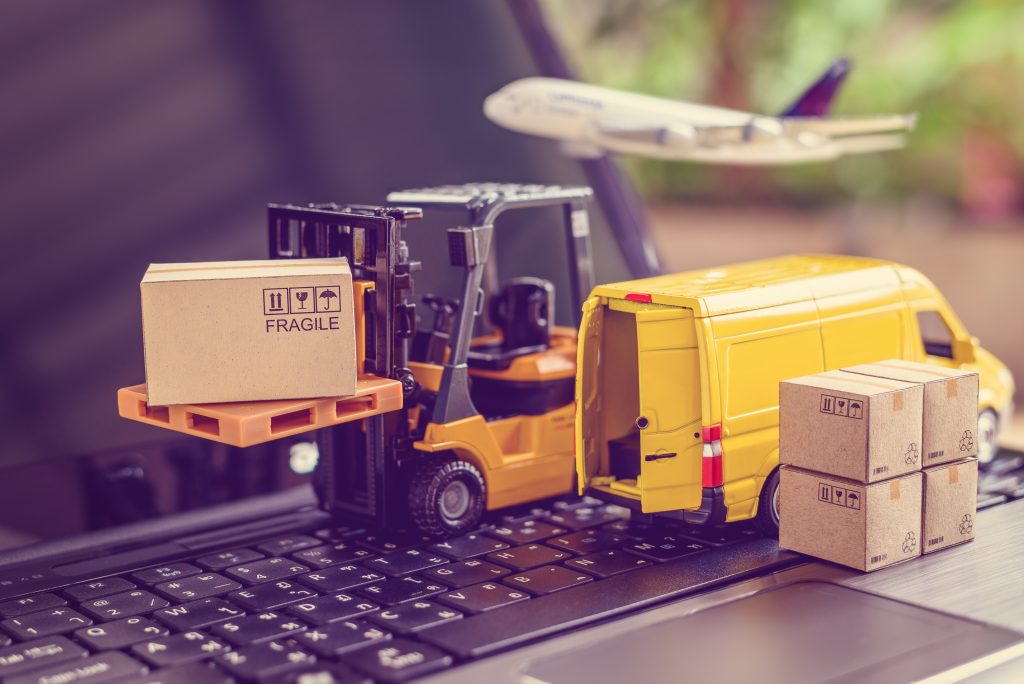
This article discusses the importance and methods of assessing a supplier’s quality in manufacturing and production processes. The article emphasizes that a supplier’s quality directly affects the final product’s quality. It categorizes supplier quality into two key aspects: their operational behavior and support towards customers and their ability to provide the best quality services, materials, components, and products needed for the buyer’s project.
The article advises that quality evaluation should start early in product development, especially for new products. It stresses the importance of involving design, purchasing, quality, and reliability teams. These teams should work together to outline the product’s requirements and goals in a Product Requirement Document (PRD), which should include specific quality standards. This collaborative approach helps select high-quality parts and find primary and secondary suppliers to ensure a continuous supply chain.
Further, small businesses might benefit from partnering with suppliers with in-house engineering resources. Such suppliers can assist in developing quality standards, especially if the business lacks the required expertise. Although possibly more costly, this collaboration ensures that critical parts meet the expected quality standards.
The article also discusses the necessity of conducting due diligence to validate a supplier’s quality. Initial checks can include examining the supplier’s website and other platforms like Alibaba and running credit report checks for financial stability and legitimacy. More advanced due diligence involves on-site audits to assess the supplier’s capabilities in design, development, production volume, testing, and quality staff adherence to standards.
Checking a supplier’s Quality Management System (QMS) is also highlighted. The article warns against taking external certifications such as ISO 9001 at face value, especially from local certifying bodies, and recommends verifying the actual implementation of these systems through onsite and remote audits and examining other quality related data from the manufacturer and perhaps other customers of the supplier.
Lastly, the article underscores the value of formalizing approved suppliers. This process involves creating a list of pre-qualified suppliers who meet the required quality, risk management, and delivery standards. Regular supplier assessments are suggested for maintaining and updating this list, ensuring a reliable and quality-focused supply chain.
Leave a Reply
You must be logged in to post a comment.