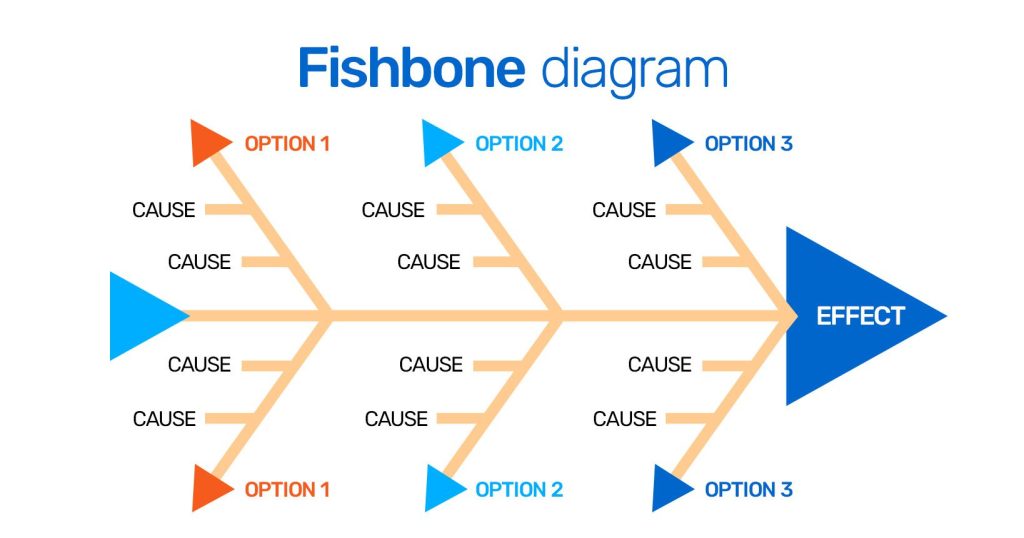
- Root cause analysis (RCA) methods like 5 Whys and Fishbone diagrams are widely used but may not effectively address the complexities of today’s work environments.
- Traditional RCA tools often lead to biased conclusions and might miss systemic issues, highlighting the need for more advanced methodologies.
- For more accurate and effective problem-solving, a holistic approach to RCA, including newer tools and deeper system-level analyses, is recommended.
In a forum discussion about root cause analysis (RCA), participants shared their experiences and concerns with traditional methods like the 5 Whys and Fishbone diagrams. They note that these tools are often applied inconsistently across industries, sometimes leading to incorrect conclusions or repeated trials to find the root cause. The discussion highlighted that these traditional tools, while still in use, may not be sufficient for tackling complex, modern-day issues, as they were developed decades ago and have not evolved significantly since.
They point that many RCA methods are outdated and prone to bias, particularly when individuals rely on their own experiences or assumptions rather than data-driven analysis. More advanced methodologies, which integrate Lean, Agile, and modern science elements, are necessary to address the complexities of today’s work environments. These newer approaches are already used in highly technical fields and are considered more efficient and accurate than traditional methods.
Another challenge is distinguishing between problems and opportunities during RCA; this distinction often needs clarification, leading to unnecessary or misdirected analyses. Others have advocated for more comprehensive approaches, such as system-level analyses, to provide a clearer understanding of root causes. Overall, RCA methods must evolve, incorporating modern tools and deeper analyses to solve problems effectively in contemporary settings.
One participant listed these key steps and limitations:
1 Confirm the Failure – So you don’t waste time chasing wild geese.
2 Remedial Action (Containment) – Keep the problem from getting worse. Stop shipment or shut down the line if necessary.
3 Clearly Define the Problem – Don’t work on the wrong problem.
4 Determine Possible Causes – Here is where a cause & effect (fishbone diagram) can help.
5 Root Cause Analysis – Here’s where the 5 Whys works well. The trick is asking the right question and knowing when to stop.
6. High level root causes are typically “rooted” in these lacking areas:
- Standard approach or plan for doing a task or accomplishing a goal.
- Capability to meet the requirements with current conditions.
- Management Support.
- Resources.
- Adequate training.
- Discipline/supervision or feedback.
Read the full article (requires ASQ membership account)
Leave a Reply
You must be logged in to post a comment.