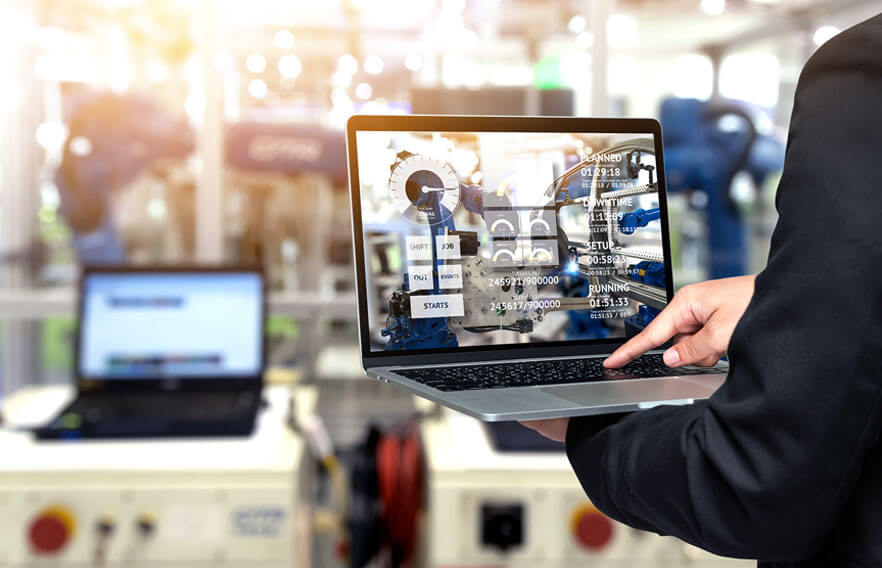
- The 8D methodology offers a structured, team-based approach to solving complex and recurring problems in manufacturing
- It includes nine steps from planning to prevention, with tools like 5 Whys and fishbone diagrams aiding root cause analysis
- Pairing 8D with an Enterprise Quality Management System (EQMS) improves collaboration, action tracking, and long-term effectiveness
The 8D (Eight Disciplines) methodology is a systematic problem-solving framework originally developed by Ford to identify and eliminate the root causes of chronic or recurring production and quality issues. Though initially intended for the automotive sector, it is widely used across industries, especially those certified under ISO 9001 or regulated by the FDA. The process begins with planning (D0), followed by eight stages: team formation, problem definition, containment, root cause identification, corrective action verification and implementation, recurrence prevention, and team recognition.
This approach is most effective for high-risk or complex issues that exceed the capabilities of simpler tools like the 5 Whys. A key strength of 8D lies in its collaborative, cross-functional nature and its emphasis on thorough root cause analysis, containment of current impacts, and systemic changes to prevent future occurrences. However, one common pitfall is focusing on action completion without ensuring the corrective measures resolved the issue, which can be addressed through scheduled effectiveness reviews months later.
Using a real-world example, the 8D method helped resolve a product odor problem by tracing the cause to heat exposure during storage. Corrective actions included layout adjustments and temperature controls, followed by verification through sampling and analytics. Integrating this methodology with an EQMS enhances its utility by centralizing documentation, automating task tracking, and enabling data-driven insights into recurring issues.
When effectively implemented with modern tools, the 8D process not only mitigates immediate quality risks but also fosters a culture of continuous improvement, accountability, and long-term operational resilience.
Leave a Reply
You must be logged in to post a comment.