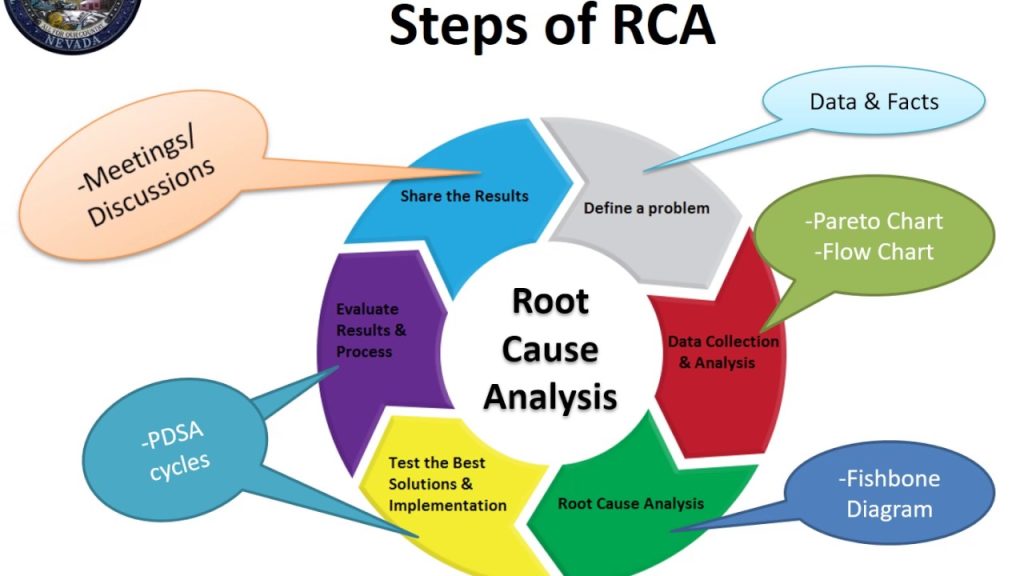
- Root cause analysis (RCA) is an essential method in quality management. It is used to diagnose the fundamental reason for faults or problems.
- Five common RCA methods are Pareto Charts, The 5 Whys, Fishbone Diagrams, Scatter Plots, and Failure Mode and Effects Analysis (FMEA).
- Employing these methods allows organizations to correct existing issues and preempt potential future problems, thereby supporting continuous improvement and quality assurance efforts.
This 36-page primer on Root cause analysis (RCA) from audit software supplier EASE covers this essential method in quality management. RCA is used to diagnose the fundamental reason for faults or problems. Five common RCA methods are Pareto Charts, The 5 Whys, Fishbone Diagrams, Scatter Plots, and Failure Mode and Effects Analysis (FMEA). This structured approach helps identify the primary causes of issues in manufacturing and other processes, which can be systematically addressed to mitigate errors and enhance product quality.
Pareto Charts help identify the most significant factors contributing to a problem, following the Pareto Principle (80/20 rule) states that 80% of problems are often due to 20% of causes. This method helps prioritize issues that need immediate attention and resource allocation. The 5 Whys method, by contrast, involves asking “why” multiple times (typically five) to peel back the layers of symptoms to reach the underlying cause. This method benefits straightforward problems and ensures solutions address the root cause rather than just the symptoms.
Fishbone Diagrams, or Ishikawa diagrams, visually represent cause and effect, organizing possible causes into categories such as People, Methods, Machines, Materials, Measurement, and Environment. This method is particularly useful in team settings for brainstorming and categorizing the causes of defects. Meanwhile, Scatter Plots can help determine correlations between different variables, aiding in verifying hypotheses generated by other RCA tools. Lastly, FMEA is an approach that anticipates potential points of failure in a process, evaluating the severity and likelihood of failures to prioritize responses.
Each of these tools has specific strengths and is suitable for different scenarios, often used in combination to ensure comprehensive problem-solving. Employing these methods allows organizations to correct existing issues and preempt potential future problems, thereby supporting continuous improvement and quality assurance efforts. These analytical tools ensure that manufacturing and production processes meet quality standards and operate efficiently.
Leave a Reply
You must be logged in to post a comment.