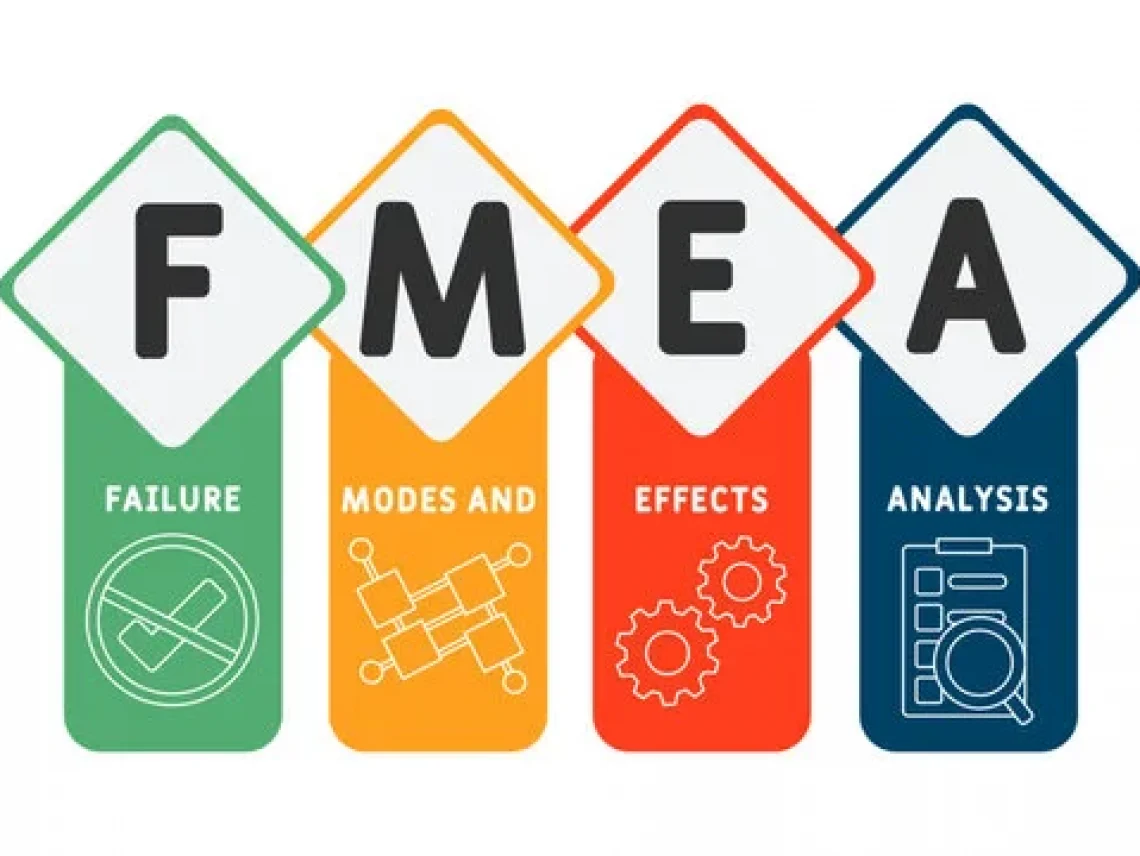
- Failure mode and effects analysis (FMEA) is evolving alongside Industry 4.0 to handle the complexities of modern manufacturing.
- Industry 4.0 technologies enhance FMEA by providing data-driven insights and enabling predictive maintenance through advanced analytics.
- Modifications in FMEA processes align it with Industry 4.0’s interconnected systems, supporting real-time decision-making and continuous improvement.
In the context of Industry 4.0, Failure Mode and Effects Analysis (FMEA) is adapting to address the increased complexity of manufacturing processes. Traditionally, FMEA assessed potential failure modes by analyzing severity, occurrence, and detection, which produced a Risk Priority Number (RPN) to guide risk mitigation efforts. However, this approach has limitations in modern Industry 4.0 environments due to its linear scoring method, which treats all parameters equally. Recent modifications, such as introducing an action priority (AP) system, emphasize severity more heavily, streamline decision-making for critical risks, and align with Industry 4.0’s advanced requirements.
The rise of Industry 4.0 technologies, including the Internet of Things (IoT) and machine learning (ML), is transforming FMEA from a static tool into a dynamic, data-driven analysis method. Integrated software now replaces traditional spreadsheet models, allowing FMEA insights to be shared instantly across interconnected systems, which can preemptively address potential failures across locations. This shift not only accelerates risk assessment but also enhances the depth of analysis, as vast volumes of data processed by ML uncover patterns and failure predictions that conventional FMEA might miss, ultimately leading to predictive maintenance and heightened asset reliability.
FMEA’s role in predictive maintenance, a key component of Industry 4.0, demonstrates its expanded utility. Using historical and real-time data, FMEA helps identify probable failures before they occur, optimizing maintenance schedules and reducing unexpected downtimes. This predictive capability, termed Predictive Maintenance 4.0 (PdM 4.0), reflects a shift from reactive to anticipatory actions, enabling manufacturing systems to self-adjust and respond to potential issues autonomously.
Finally, Industry 4.0 presents new challenges and opportunities for FMEA, particularly regarding data precision and analytical models. Traditional FMEA relies on human interpretation, which can introduce biases. To address this, fuzzy set theory and gray systems are emerging to handle ambiguities and provide more accurate failure predictions. By integrating these advanced analytical approaches, FMEA can more effectively navigate the uncertain and interconnected nature of modern manufacturing, paving the way for its continued relevance and utility in the Industry 4.0 era.
Read the full article (requires free ASQ login credentials)
Leave a Reply
You must be logged in to post a comment.