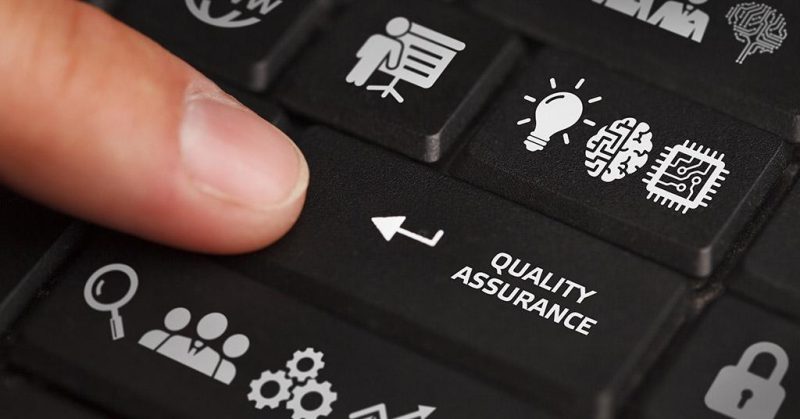
- Quality assurance (QA) focuses on proactive measures to prevent defects by optimizing processes, while quality control (QC) is reactive, ensuring that final products meet established standards through inspections and testing.
- Effective quality management integrates QA and QC by incorporating customer feedback, setting measurable quality standards, and continuously analyzing production data to identify and resolve potential issues.
- QA and QC are crucial across industries such as software development, food production, and manufacturing, ensuring security, safety, and reliability through systematic controls and continuous improvement efforts.
Quality assurance (QA) and quality control (QC) are often confused but serve distinct roles in ensuring product and service quality. QA is a proactive approach that focuses on process optimization and defect prevention, incorporating customer feedback and continuous evaluation to maintain high standards. It extends beyond pre-production planning to monitor the entire product lifecycle, ensuring that organizational processes align with established quality objectives. Meanwhile, QC is a reactive process that involves monitoring, measuring, and controlling product quality through inspections, audits, and statistical analyses to detect and address defects before they reach customers.
Key elements of an effective quality management system include setting clear quality standards, utilizing data-driven decision-making, and continuously analyzing QC results to refine processes. Organizations use methods such as in-process inspections, document control, and supplier quality management to maintain consistency and compliance. Statistical process control (SPC), Six Sigma, and the Taguchi Method are commonly applied to minimize defects and enhance operational efficiency. Feedback loops from customers and internal stakeholders help drive continuous improvement, ensuring that products evolve to meet changing expectations and regulatory requirements.
QA and QC play a critical role across multiple industries. In cybersecurity, QA ensures software security through penetration testing and code reviews, preventing vulnerabilities that could lead to data breaches. In food production, rigorous QC measures, such as microbiological testing and supply chain verification, safeguard consumer health. In manufacturing, real-time monitoring and automated inspections help maintain product consistency and reduce defects. By integrating QA and QC methodologies, businesses can enhance customer satisfaction, maintain regulatory compliance, and achieve long-term operational success.
Leave a Reply
You must be logged in to post a comment.