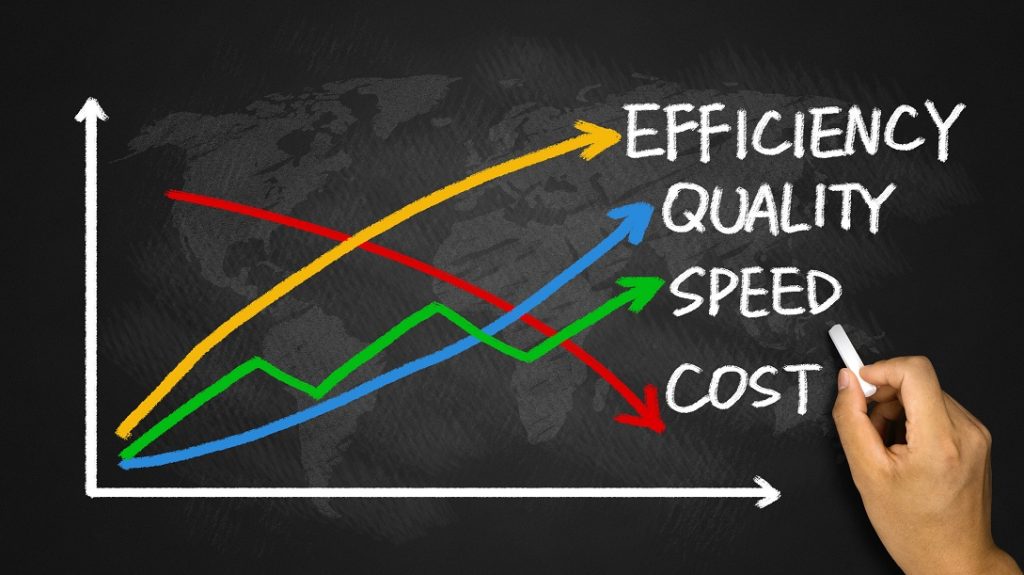
- Productivity gains remain elusive due to misguided reliance on automation to cut headcount rather than improve processes
- U.S. government and corporations often ignore the root causes of inefficiency by automating without understanding work systems or engaging frontline employees
- Sustainable productivity improvements stem from lean principles, human-centered process design, and collaboration between people and technology
The failure of automation-driven strategies to deliver promised productivity gains, known as the “productivity paradox,” stems from a flawed approach that prioritizes cutting labor costs rather than improving value creation. This mindset, rooted in outdated ROI models and managerial assumptions, leads to the replacement of workers with technology without fully understanding or improving the underlying work processes. Such short-term cost-cutting measures have failed to boost total factor productivity (TFP), which has stagnated in the U.S. economy despite decades of technological investment.
Attempts to automate without process insight, such as GM’s failed “factory of the future” or the Department of Government Efficiency’s recent AI-driven mass layoffs, highlight the dangers of treating employees as disposable costs. Financial metrics often obscure the true productivity drivers, such as process efficiency, defect reduction, and employee morale. In contrast, organizations like Toyota and Parker Hannifin demonstrate how productivity can steadily improve when automation supports, rather than replaces, people, following structured process improvements and lean principles before considering robotics.
Collaborative robotics (cobots), which assist rather than displace workers, exemplify a more productive approach to automation. Companies like Universal Robots emphasize empowering employees to own and adapt the technology, integrating it into simplified and improved workflows. This collaborative mindset aligns with Industry 5.0 principles, which prioritize human and environmental well-being alongside technological advancement.
True productivity improvement depends on a deep understanding of work processes and respect for those performing them. Leaders who engage employees in redesigning workflows and use automation strategically—as a complement rather than a substitute—are far more likely to generate meaningful and sustainable performance gains.
Leave a Reply
You must be logged in to post a comment.