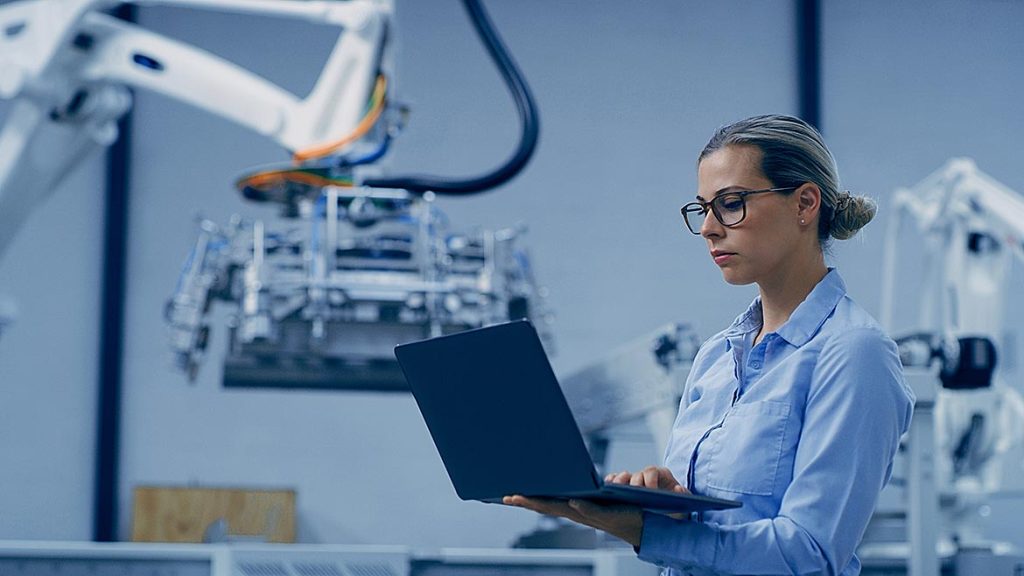
This article introduces a new concept called Learning Quality Control (LQC), an evolution of Statistical Quality Control (SQC). LQC is a process monitoring system that leverages machine learning and deep learning to enhance quality control in manufacturing. It focuses on real-time defect prediction or detection using historical samples, which include process measurements and binary quality labels. The system is trained to automatically detect patterns associated with defects, such as anomalies, deviations, and non-conformances.
The article explains the classification process of LQC, which involves comparing predicted probabilities to a classification threshold. The performance of this classifier is summarized using concepts such as True Positive, True Negative, False Positive, and False Negative, illustrated in a confusion matrix. LQC’s main challenge in the Quality 4.0 era is to detect or prevent the few defects in datasets that are usually highly imbalanced, containing many good quality items and few defects.
The article also highlights two critical concepts in LQC: offline learning, where historical data is used to train machine learning algorithms, and online deployment, where the classifier is implemented in production to detect quality defects in real-time. For example, the system would automatically see whether a weld is good or defective in a welding process. The article stresses that minimizing False Negatives is crucial, as these undetected faulty items could lead to customer complaints or warranty events.
Lastly, the article presents case studies to illustrate LQC’s applications. One case study uses structured data to show how machine learning algorithms can identify patterns in high-dimensional spaces that typical control charts cannot detect. Another case study demonstrates LQC’s application in replacing visual-based monitoring systems, using convolutional neural networks to monitor processes and detect defects. The article concludes that Quality 4.0 does not replace Six Sigma but enhances the quality movement, requiring quality engineers to integrate these concepts for breakthrough innovations in manufacturing.
Leave a Reply
You must be logged in to post a comment.