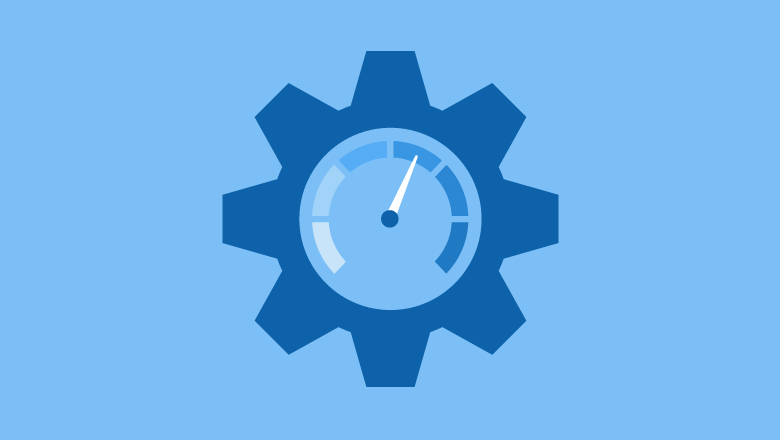
- Identifying internal and external issues and understanding the needs of interested parties are critical steps in optimizing your Quality Management System (QMS) under ISO 9001:2015.
- Effective strategies, such as SWOT analysis, PESTLE analysis, and stakeholder engagement, can help address these aspects, while QMS software tools can streamline the process and enhance compliance and efficiency.
- Using dedicated QMS software modules, such as internal audits, risk management, and customer feedback systems, ensures that your QMS remains robust, adaptable, and aligned with both internal needs and external expectations.
ISO 9001:2015 provides a structured framework for managing and improving the quality of business processes by focusing on internal and external factors that impact a Quality Management System (QMS). One of the key elements of this standard is understanding how these factors and interested parties influence your ability to meet objectives and ensure success.
To optimize your QMS, it’s essential to identify and address internal issues, such as organizational culture and resources, and external issues like market trends and regulatory changes. Additionally, understanding the needs of interested parties—such as customers, suppliers, and regulatory bodies—is crucial for maintaining a high quality standard and achieving consistent performance.
Internal issues can be identified through employee feedback, SWOT analysis, and management reviews, which help pinpoint strengths, weaknesses, and areas for improvement. External issues are best understood through tools like PESTLE analysis, monitoring regulatory updates, and staying informed about industry trends.
Recognizing the needs of interested parties involves stakeholder analysis, regular communication with key customers and suppliers, and a thorough review of industry standards and regulations. These steps ensure that your QMS is aligned with the expectations of those who have a stake in your business’s success.
By correctly executing these strategies, you can create a more effective, responsive, and sustainable Quality Management System that meets the demands of both internal operations and external environments.
Leave a Reply
You must be logged in to post a comment.