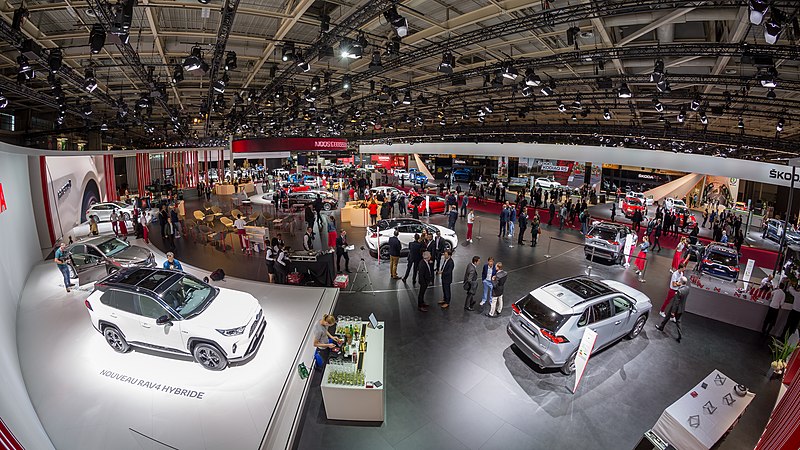
- The GD3 approach, standing for “good discussion, good dissection, good design,” revolutionizes the traditional approach to addressing quality issues by anticipating and designing out potential problems before they occur.
- GD3 is not just about technicalities but also embraces a social aspect, emphasizing the importance of cross-functional collaboration and open communication within the organization.
- Toyota’s consistent record of high-quality production is partly attributed to implementing GD3, which underscores the company’s unwavering dedication to customer satisfaction and quality-first mindset.
Jim Morgan and Matthew Savas delve into the transformative GD3 method in product development, a methodology pioneered by Toyota to elevate product quality and customer satisfaction while minimizing costs and avoiding failures. The GD3 approach, standing for “good discussion, good dissection, good design,” revolutionizes the traditional approach to addressing quality issues by anticipating and designing out potential problems before they occur. This method was developed by Professor Tatsuhiko Yoshimura, a key figure in Toyota’s quality system, who, after extensive research and frustration with existing quality methodologies like FMEA, sought inspiration from other disciplines, including industrial accident prevention. His insights led to the development of GD3, drawing parallels between mitigating safety risks and preempting quality issues in product designs.
GD3 is not just about technicalities but also embraces a social aspect, emphasizing the importance of cross-functional collaboration and open communication within the organization. The method encourages meticulous examination of product designs to identify and address “hidden problems,” utilizing principles such as robust design reuse, cross-functional analysis, and detailed dissection of test results. This holistic approach aims to uncover potential design flaws early on, facilitating more efficient and effective problem-solving. GD3’s emphasis on good discussion aims to foster a culture where potential issues are openly discussed and collaboratively solved rather than concealed or ignored, aligning closely with Toyota’s customer-centric philosophy and commitment to continuous improvement.
Toyota’s consistent record of high-quality production is partly attributed to implementing GD3, which underscores the company’s unwavering dedication to customer satisfaction and quality-first mindset. The method’s success lies in creating a transparent and rigorous organizational culture that actively seeks out and addresses big and small problems, ensuring they don’t escalate into quality crises. For organizations aspiring to improve their quality management practices, adopting the GD3 methodology—or elements tailored to their specific needs—can pave the way towards achieving superior product quality and fostering a culture of transparency, customer focus, and relentless pursuit of excellence.
Leave a Reply
You must be logged in to post a comment.