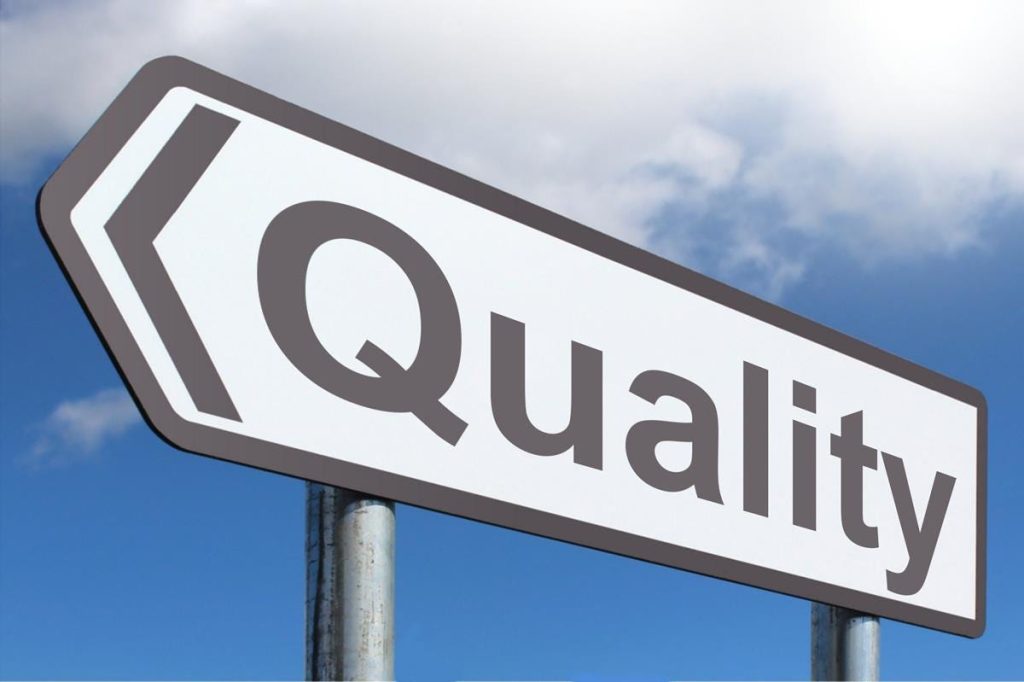
- The study aims to explore the critical failure factors (CFFs) associated with the implementation of Q4.0 and how its failure can be measured.
- The concept of Q4.0, being at a nascent stage, has not been extensively covered in existing literature, making this article valuable for businesses trying to understand and mitigate potential problems in their Q4.0 initiatives.
- The study significantly contributes to the understanding of Q4.0, particularly in identifying its benefits, the types of Q4.0 projects being implemented, and the training needs for its successful deployment.
This academic article, published in the International Journal of Quality & Reliability Management, delves into Quality 4.0 (Q4.0), a new concept in the field of quality management. The study aims to explore the critical failure factors (CFFs) associated with the implementation of Q4.0 and how its failure can be measured. This qualitative study involved in-depth interviews with quality managers and executives to establish the CFFs for Q4.0. The findings highlighted resistance to change, a lack of understanding of Q4.0 as significant CFFs, and a complete lack of training on Q4.0. The concept of Q4.0, being at a nascent stage, has not been extensively covered in existing literature, making this article valuable for businesses trying to understand and mitigate potential problems in their Q4.0 initiatives.
In their exploration, the authors found that Q4.0 is closely aligned with Industry 4.0 technologies and aims to improve customer satisfaction and the quality of products and services. It has been noted that Q4.0 can reduce quality costs while increasing revenues and reducing supplier defect rates. The study identifies a significant knowledge gap in the Q4.0 sector. It suggests that sustainable growth can be achieved when organizations are aware of the CFFs and how quality standards link to quality initiatives.
The study identified critical failure factors (CFFs) of Quality 4.0 (Q4.0) through a qualitative approach and explored necessary training and competencies for its implementation. It contributed to discussions on the relationship between Q4.0 and ISO 9001 standards, revealing that Q4.0 deployment is still early. Key findings include the lack of formal education for Q4.0 implementation teams and the absence of supportive educational programs. Primary CFFs include inadequate leadership support, strategic misalignment, insufficient knowledge and training of Q4.0, a dearth of professionals skilled in Q4.0, and poor change management.
The study significantly contributes to the understanding of Q4.0, particularly in identifying its benefits, the types of Q4.0 projects being implemented, and the training needs for its successful deployment. It also highlights the importance of leadership support, adequate planning and strategy, and addressing human factors like resistance to change for successful Q4.0 implementation. The findings of this study offer valuable insights for organizations aiming to integrate Q4.0 into their quality management strategies, providing a deeper understanding of integrating Q4.0 with quality standards for knowledge management.
Leave a Reply
You must be logged in to post a comment.