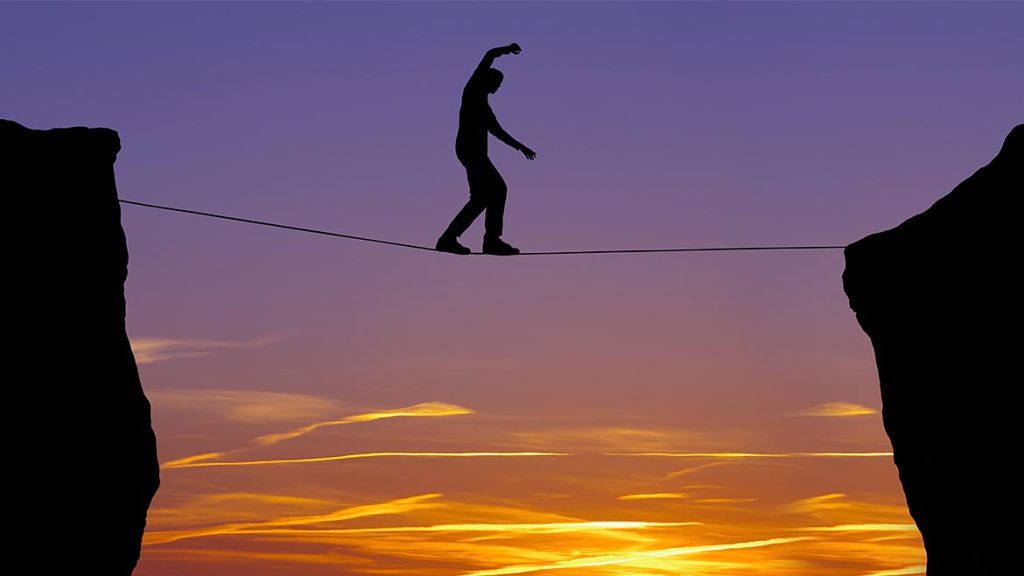
In this article, Ian Lazarus discusses the challenges of balancing customer satisfaction, stakeholder interests, and budget constraints in process improvement and design. Lazarus starts by addressing the dilemma of creating enduring quality in products and processes, particularly when faced with the desire for rich and flexible design. He points out that simply saying “no” to customer demands isn’t always feasible, as it could lead to product or process development stagnation.
Lazarus emphasizes that processes are dynamic and highlights the importance of considering the customer’s perspective in process design. He uses the example of an emergency room to illustrate how processes often evolve for the convenience of the staff rather than the customers. He recounts his experience working with a health system to redesign their women’s surgical suite and maternity ward, where he encountered resistance from a nurse who focused more on her convenience than patient needs. This example underlines the common issue in many businesses where the evolution of processes becomes institutionalized without adequate consideration of the customer’s experience.
The article also delves into the issue of staff designing their approaches to service delivery, often overlooking what might be best for the customer. Lazarus refers to “Little’s Law,” which relates to the performance of multiple processes and their impact on cycle time or waiting time. He explains how varying approaches can lead to inefficiencies, as demonstrated by more prolonged waiting times in services like call centers. The ideal scenario is where staff align around best practices to ensure efficiency and customer satisfaction.
Lazarus concludes by applying these concepts to emergency room operations, where exceeding capacity often leads to patient diversion rather than addressing the root cause of the problem. He advocates for understanding and eliminating variations that cause inefficiencies and aligning processes with higher production levels. This approach is integral to Lean and Six Sigma methodologies, which he plans to explore further in his next column, focusing on overcoming the final obstacle to successfully implementing these methods.
Leave a Reply
You must be logged in to post a comment.