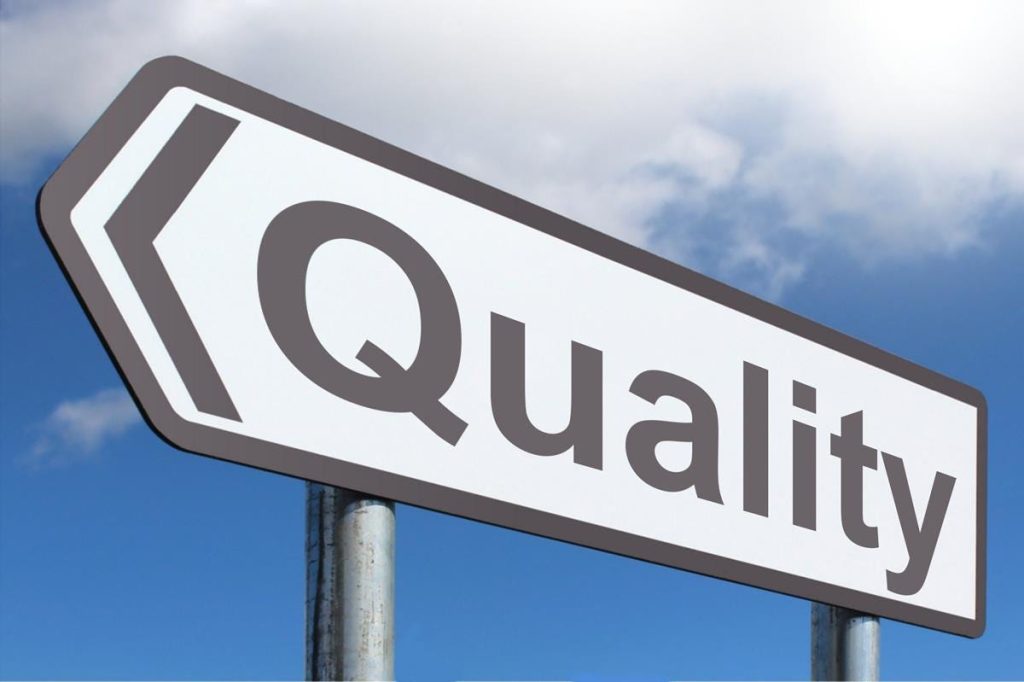
- Quality metrics in manufacturing are categorized into process, product, maintenance, and supplier quality metrics, each serving a specific role in improving operational efficiency and reducing defects.
- Key metrics include cost of quality, defect rates, customer complaints, scrap rates, yield, overall equipment effectiveness (OEE), throughput, and supplier quality, helping organizations enhance production reliability and stakeholder satisfaction.
- Implementing these metrics requires clear objectives, relevant data collection, and continuous monitoring, ensuring quality assurance (QA) improvements and overall manufacturing excellence.
Measuring quality metrics in manufacturing is essential for identifying inefficiencies and improving product standards. These metrics are divided into process metrics (evaluating production efficiency), product metrics (assessing defect rates and customer satisfaction), maintenance metrics (ensuring equipment reliability), and supplier quality metrics (monitoring material quality). Categorizing these indicators helps manufacturers pinpoint critical areas for improvement and align with industry best practices.
Among the most crucial metrics, the cost of quality (CoQ) tracks expenses related to both defect prevention and failures, helping businesses prioritize cost-effective improvements. Defect rates, measured through defective parts per million (DPPM) or defects per million opportunities (DPMO), identify weak points in production. Customer complaints, scrap rates, and first-pass yield (FPY) highlight areas where product quality can be optimized. Metrics like overall equipment effectiveness (OEE) and throughput provide insights into machine efficiency and production bottlenecks, while supplier defect rates ensure high-quality inputs from vendors.
Implementing quality metrics requires setting clear objectives, selecting relevant KPIs, leveraging data collection tools, and continuously monitoring progress. Companies must balance leading indicators (which predict future performance) with lagging indicators (which reflect past outcomes) to drive continuous improvement. By strategically applying these metrics, manufacturers can enhance quality assurance, reduce waste, and meet increasing market expectations.
Leave a Reply
You must be logged in to post a comment.