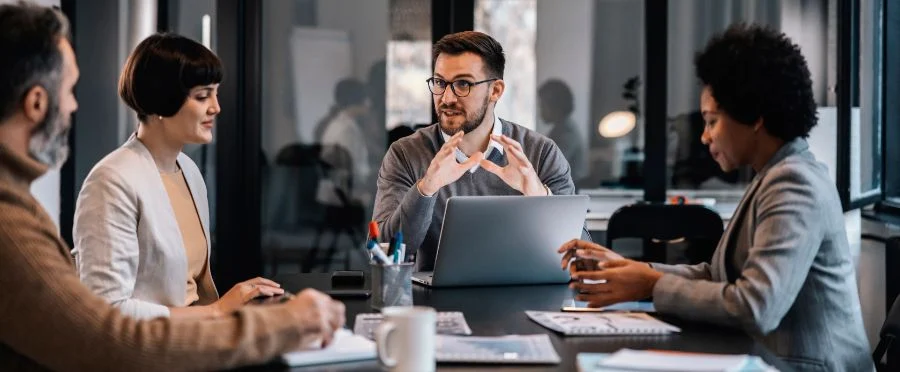
- Six Sigma projects often fail due to lack of leadership buy-in, resistance to change, poor data quality, absence of success stories, and the time-intensive nature of the methodology.
- To overcome these pitfalls, organizations should align Six Sigma with strategic goals, provide robust training, promote transparency, and invest in high-quality data collection.
- Success requires both leadership commitment and a supportive culture that encourages continuous improvement and knowledge sharing.
Despite its reputation as an effective process improvement methodology, Six Sigma can fall short of expectations for several reasons. One of the primary barriers is a lack of buy-in from senior leadership. Six Sigma projects struggle to secure resources, align with organizational goals, or gain traction without the necessary support. Additionally, the time-sensitive nature of Six Sigma can be problematic, as its methodical approach may not align with companies seeking quick results. This tension can reduce the commitment to long-term improvements. Moreover, resistance to change within an organization is common when implementing Six Sigma. Employees may be reluctant to adopt new methods, fearing disruption to their roles or routines.
Another key challenge is the absence of success stories. Organizations without tangible examples of Six Sigma’s impact may become skeptical of its potential. Pilot projects that demonstrate quantifiable results can help address this issue. Finally, the lack of high-quality data can derail Six Sigma efforts. Poor data leads to faulty analysis, making it difficult to make informed decisions and measure progress accurately. Ensuring that reliable, standardized data collection is in place is essential for the success of any Six Sigma initiative.
Overcoming these pitfalls requires strategic leadership, clear communication, and a culture of continuous improvement. Organizations can ensure the success of their Six Sigma initiatives by aligning Six Sigma projects with organizational goals, securing leadership support, investing in proper training, and emphasizing the importance of high-quality data.
Leave a Reply
You must be logged in to post a comment.