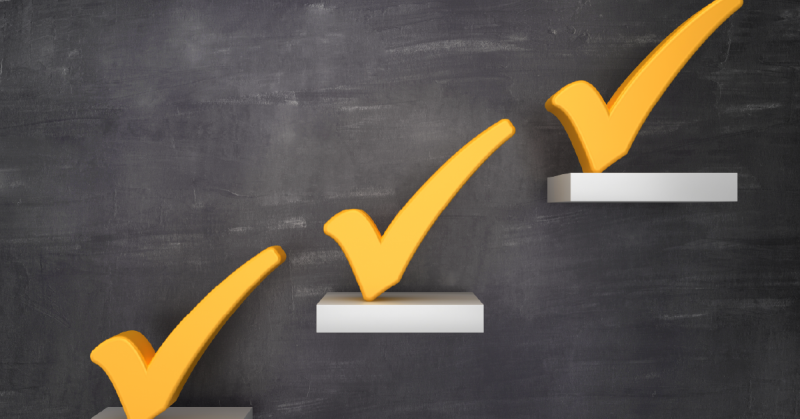
For quality professionals and non-quality professionals who may have not delved into Lean Six Sigma (LSS), this article provides a good summary. The LSS methodology combines the principles of Lean (focusing on reducing waste and inefficiency) and Six Sigma (aiming to minimize defects and variations in processes). LSS is described as a data-driven process improvement methodology and project management structure, streamlining operations, enhancing quality, and increasing efficiency. Initially adopted by Motorola in the 1980s, LSS has saved billions of dollars in various industries, from manufacturing to healthcare and finance. It has shown its adaptability across diverse sectors, optimizing manufacturing processes, financial services, and patient care in healthcare.
LSS operates on the DMAIC process (Define, Measure, Analyze, Improve, Control), a structured approach for continuous improvement and problem-solving. This process involves clear project definitions, systematic data collection and analysis, root cause analysis, solution testing, change management, continuous monitoring, involvement of cross-functional teams, training and education, thorough documentation, and celebrating success. These practices ensure sustainable process improvements.
The methodology combines two distinct approaches: Lean Manufacturing and Six Sigma. Lean Manufacturing, developed in the early 20th century with the Toyota Production System, focuses on reducing waste and improving efficiency. Six Sigma, developed by Motorola and popularized by General Electric, aims to reduce product defects. Integrating these two approaches, Lean Six Sigma addresses quality and efficiency, evolving beyond its manufacturing roots to various industries.
Lean Six Sigma principles revolve around focusing on the customer, measuring the value stream, removing waste, eliminating variations, systematic improvements, empowering people in processes, and understanding the workflow. The methodology follows the DMAIC improvement cycle, consisting of the Define, Measure, Analyze, Improve, and Control stages, each supported by specific tools and techniques. Lean Six Sigma also uses a “belt” system to designate levels of expertise and responsibilities within the methodology, ranging from White Belt to Master Black Belt. The benefits of implementing Lean Six Sigma include increased efficiency and productivity, improved quality, enhanced employee engagement and development, reduced costs, and increased customer satisfaction.
Lean Six Sigma training costs vary depending on the training level, provider, and program. It ranges from affordable online courses to more expensive classroom-based training, with additional certification fees. The article concludes by emphasizing Lean Six Sigma’s role in enhancing organizational efficiency, quality, and profitability, positioning it as a strategic imperative for businesses seeking to maintain a competitive edge in today’s marketplace.
Leave a Reply
You must be logged in to post a comment.