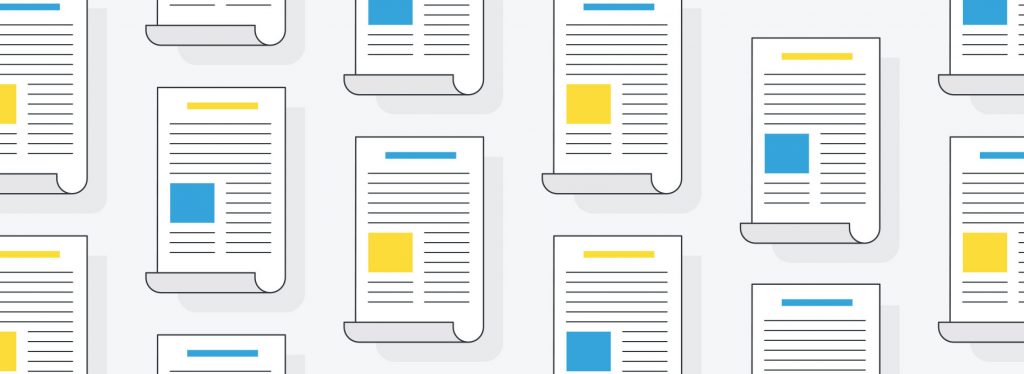
So, how is your standardized work (SW) implementation going?
Responses to that usually paint an ugly picture. Here’s what I frequently hear:
- “We just don’t have the discipline Toyota has to make SW work.”
- “We put it in place, but the people don’t follow it.”
- “We have trouble transferring good SW from one worksite to another.”
- “We are good at determining the One Best Way, but people always insist on doing it their way.”
- “People just don’t want to follow it. They like to do their own thing.”
- “We put in an audit process, but the auditors don’t follow the audit process.”
I like to say that the Toyota Way is a socio-technical system on steroids. A test for all our lean systems is how well we integrate people with process (the social with the technical). Nowhere does that come together more than in the form of standardized work and kaizen.
By that, I’m saying much more than just pointing out that our corporate-level lean initiatives should involve both Engineering and Human Resources departments, each initiating programs to elevate the technical and the social dimensions of work. I am talking about how work design simultaneously embodies both dimensions at the micro level. When a worker bolts in the seat belt in the factory or an office staffer processes a requisition in the office, the work will be driven by both the technical and social aspects of the job design.
Leave a Reply
You must be logged in to post a comment.