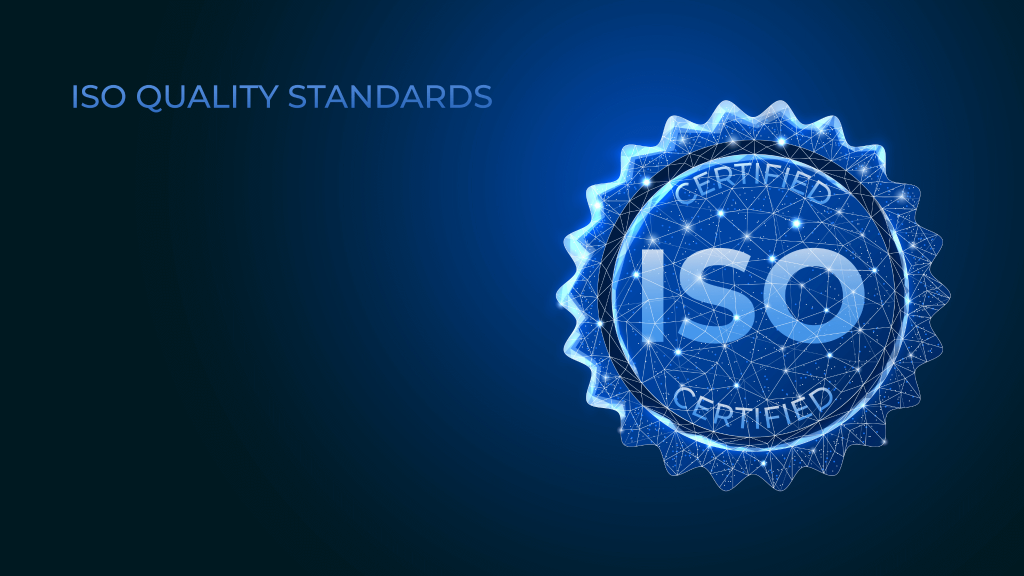
- ISO 9001 and Lean principles align closely, emphasizing process structure, continuous improvement, and efficiency.
- Companies should integrate both methodologies to enhance quality, reduce waste, and create a structured, adaptable system.
- A culture of ongoing implementation, monitoring, and adjustment ensures that ISO certification delivers real value beyond compliance.
This podcast explores the synergy between ISO 9001 and Lean methodologies, emphasizing how they complement one another in improving quality management and operational efficiency. While ISO 9001 provides a structured framework for quality assurance, Lean principles focus on waste reduction and continuous improvement. Organizations that integrate both approaches can create more efficient workflows, maintain high-quality standards, and enhance customer satisfaction.
A key takeaway is that ISO 9001 should not be viewed as a bureaucratic burden but rather as a tool to drive efficiency and consistency. The Plan-Do-Check-Act (PDCA) cycle in ISO 9001 aligns well with Lean’s continuous improvement mindset, making them natural partners in process optimization. Companies aiming for ISO certification should embed its principles into daily operations rather than treating it as a one-time compliance exercise.
For businesses new to both Lean and ISO 9001, starting with ISO’s structured framework can provide a foundation for later Lean implementation. However, organizations already applying Lean principles may find ISO certification relatively quick to achieve. Ultimately, the success of both methodologies depends on leadership commitment, workforce engagement, and a culture that prioritizes continuous learning and process refinement.
Leave a Reply
You must be logged in to post a comment.