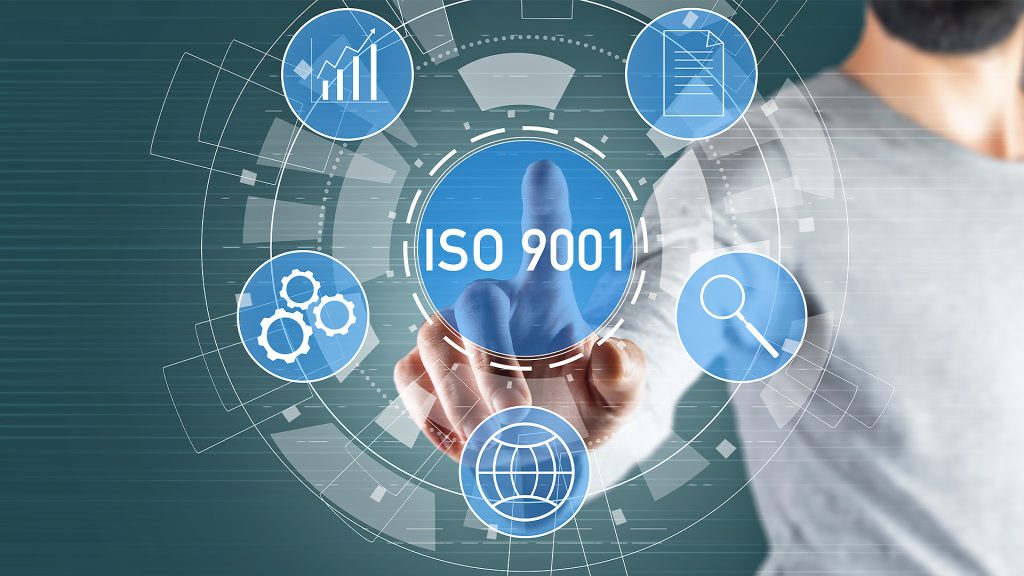
- Understanding and implementing Clause 4.4 of ISO 9001 is essential for creating a robust Quality Management System that ensures all processes contribute effectively to customer and regulatory requirements.
- Key steps in implementing Clause 4.4 include identifying and mapping processes, understanding process interactions, setting criteria and methods, applying risk-based thinking, assigning resources, monitoring performance, and driving continuous improvement.
- Common challenges in implementing Clause 4.4 include unclear process interactions and insufficient stakeholder involvement, which can be addressed through thorough process mapping and active engagement of all relevant parties.
Clause 4.4 of ISO 9001 is crucial for developing a robust Quality Management System (QMS), yet many organizations struggle to grasp its requirements fully. This clause emphasizes a process-based approach to ensure all activities within a company contribute effectively to meeting customer and regulatory requirements. A well-executed QMS, grounded in this clause, helps meet regulatory standards and provides consistent and reliable customer satisfaction.
The implementation of Clause 4.4 involves several key steps:
- Identifying and Mapping Processes: Identify critical processes and differentiate between management, support, and core processes. Visual tools like flowcharts and SIPOC diagrams are invaluable in mapping these processes, helping to pinpoint key roles and potential bottlenecks.
- Determining Process Interactions: Understanding how different processes interact is essential for a unified QMS. Visual aids like flowcharts can demonstrate process dependencies and help manage risks, ensuring smooth operations across the business.
- Establishing Criteria and Methods: Set clear success criteria for processes, such as production output or customer satisfaction rates, and choose appropriate methods to control these processes. This helps maintain consistency and high quality.
- Risk-Based Thinking: Incorporate risk assessments to identify and mitigate potential problems before they escalate. This proactive approach strengthens overall safety and quality standards.
- Assigning Resources and Responsibilities: Proper resource allocation and clear role definitions are critical to a QMS’s success. Assigning specific responsibilities ensures accountability and smooth process execution.
- Monitoring, Measurement, and Analysis: Regularly monitor and measure process performance using Key Performance Indicators (KPIs) to evaluate effectiveness and identify areas for improvement.
- Process Improvement: Continuous improvement is at the heart of ISO 9001. Methods like PDCA, Lean, and Six Sigma help identify inefficiencies, reduce defects, and enhance overall process quality. Encouraging a culture of continuous improvement is vital for long-term success.
Clause 4.4 is the foundation of a robust QMS, providing a structured approach to process identification, interaction, and improvement. By embracing a risk-based approach and actively involving all stakeholders, organizations can develop effective QMS processes that drive consistent quality and customer satisfaction.
Leave a Reply
You must be logged in to post a comment.