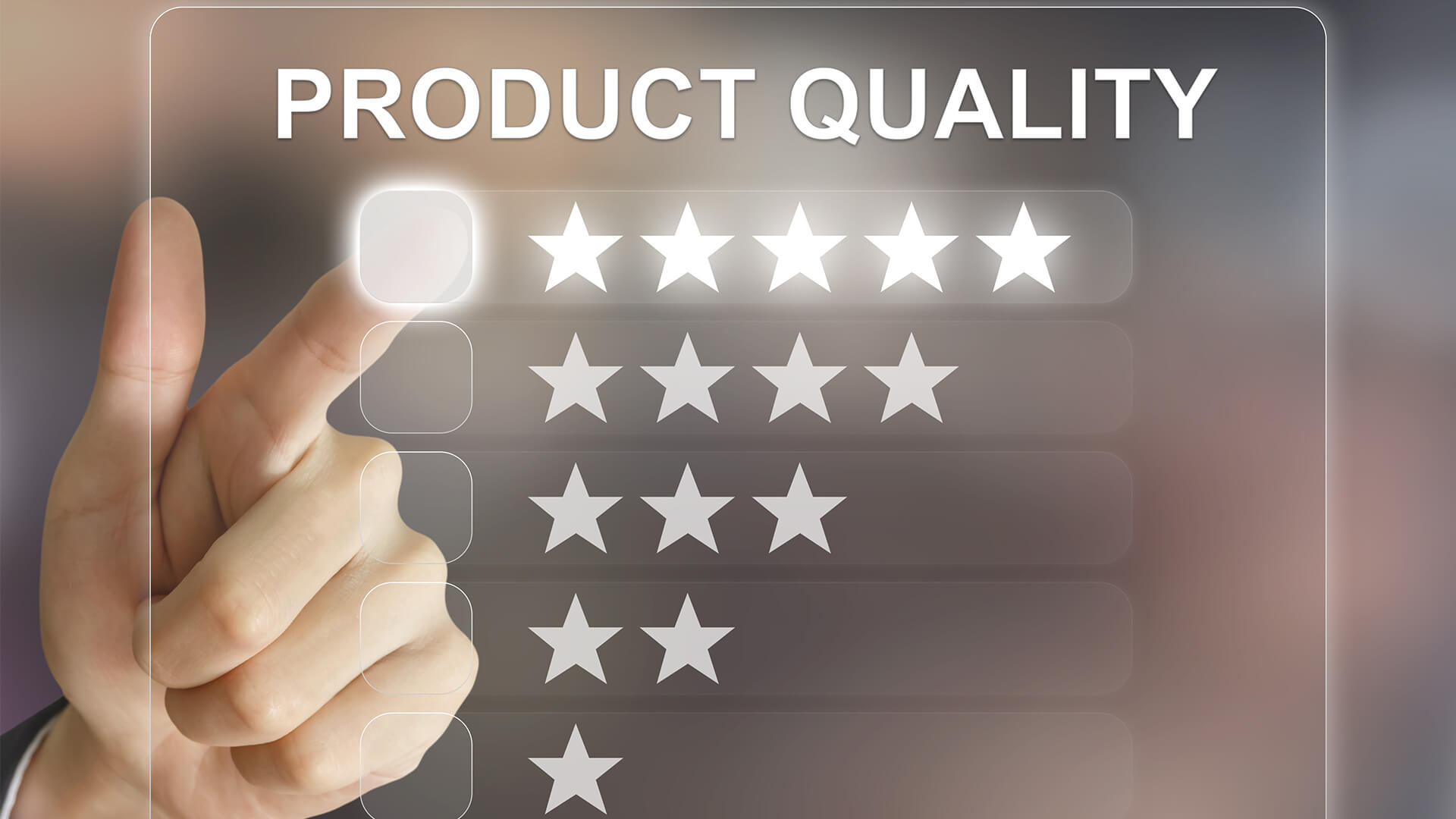
- Implementing Corrective and Preventive Action (CAPA) and New Product Development and Introduction (NPDI) in a Quality Management System (QMS) enhanced product quality by proactively addressing root causes and embedding quality from the design stage.
- CAPA integration involved systematic root cause analysis (RCA) using tools like FMEA and Ishikawa diagrams, supported by a dedicated review board for consistent oversight.
- NPDI integration can ensure early detection of design flaws through cross-department collaboration, minimizing post-launch issues and reinforcing continuous improvement.
This case history describes a journey to improving product quality through a Quality Management System (QMS) which began with a proactive approach to persistent quality challenges. Initially, a reactive response led to recurring issues that eroded customer confidence. This experience highlighted the need for a structured approach, integrating CAPA (Corrective and Preventive Actions) and NPDI (New Product Development and Introduction) into a cohesive QMS. Starting with a thorough assessment, the process aimed to address systemic issues, identify root causes, and prevent future occurrences.
Securing executive support was crucial, allowing for resources and personnel to be allocated for QMS development. A cross-functional team representing key departments was formed to foster a collaborative approach to problem-solving. CAPA was implemented with a focus on standardized documentation, RCA practices, and consistent training. Tools such as FMEA and Ishikawa diagrams were applied to diagnose and prioritize issues, transforming CAPA into an integral part of quality improvement rather than a reactive fix.
The QMS also incorporated NPDI to ensure quality was considered from the outset of product development. This collaboration enabled early identification of design flaws, reducing the need for costly post-launch fixes. Testing and validation were prioritized, especially under time constraints, by adopting a risk-based approach to balance market demands with quality standards.
Challenges included resistance to change and maintaining consistency across departments, addressed through clear communication, training, and standardization of CAPA practices. Even after implementation, continuous improvement remains a core principle, with plans to leverage data analytics and machine learning for predictive insights. The QMS journey underscored the value of CAPA and NPDI in enhancing quality, reducing issues, and fostering a culture of innovation and improvement.
Leave a Reply
You must be logged in to post a comment.