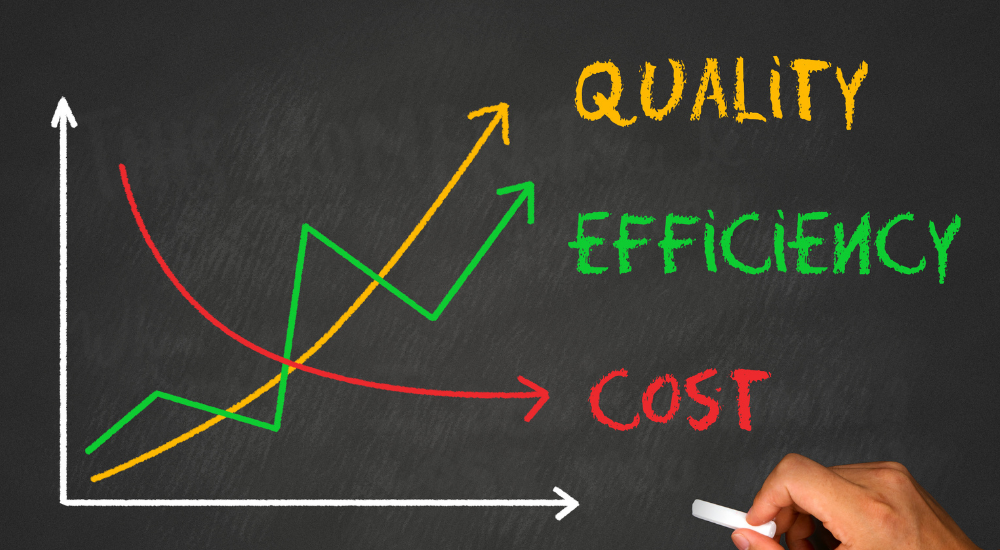
- One common way to reduce the Cost of Poor Quality (CoPQ) is to leverage the 1-10-100 rule, which highlights the exponential savings realized when issues are caught early.
- The key takeaway for manufacturers is that reducing quality costs requires a proactive shift toward prevention.
- Implementing automated systems can help organizations improve reliability, meet customer expectations, and minimize the financial and reputational risks associated with quality failures.
Manufacturers across various industries, from aerospace to medical devices, face immense pressure to ensure product quality and avoid costly defects. The average cost of a significant product recall can reach $12 million, possibly even larger sums when factoring in reputational damage. Despite these risks, many manufacturers miscalculate their total cost of quality (TCoQ), often overlooking hidden expenses related to poor quality (CoPQ). Only 17% of companies fully understand their TCoQ, according to LNS Research. This misunderstanding can lead to underinvestment in critical areas like prevention and early detection, essential for minimizing CoPQ.
One common way to reduce CoPQ is by leveraging the 1-10-100 rule, highlighting the exponential savings realized when issues are caught early. For every $1 spent on prevention, a company saves $10 on appraisal and $100 on failure costs. Investing in strategies like Layered Process Audits (LPAs) can help manufacturers detect and prevent defects before they escalate into costly problems. LPAs engage multiple levels of the organization in frequent, high-impact audits, reducing production variability and enhancing process control.
Automation plays a critical role in the success of LPA programs. By automating these audits with certain platforms, manufacturers can increase completion rates, improve decision-making through real-time data, and reduce administrative burdens. Automation also helps track and address corrective actions faster, reducing backlogs and preventing quality escapes.
Companies that invest in LPAs and prevention strategies see significant returns. One automotive supplier reduced internal defects by 73%, cut overdue corrective actions by 94%, and achieved 85% or higher audit completion rates. As digital transformation becomes more prevalent, early adopters of Quality 4.0 technologies defy traditional cost trends, continuously reducing CoGQ and CoPQ.
The key takeaway for manufacturers is that reducing quality costs requires a proactive shift toward prevention. Implementing automated systems can help organizations improve reliability, meet customer expectations, and minimize the financial and reputational risks associated with quality failures.
Leave a Reply
You must be logged in to post a comment.