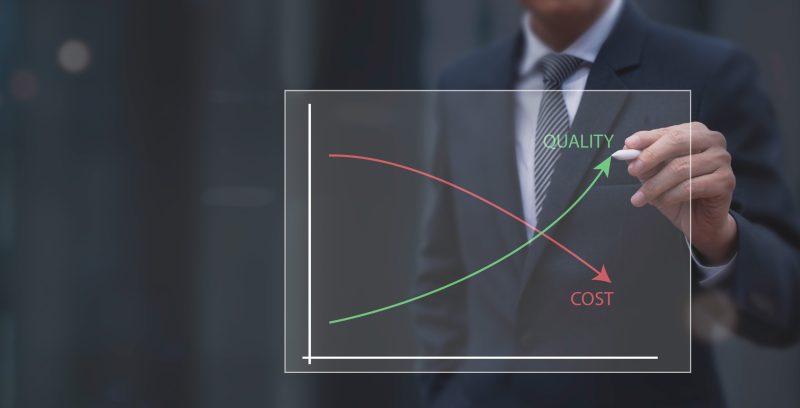
- The Cost of Quality (CoQ) consists of the costs of conformance (preventing defects) and non-conformance (fixing defects), impacting profitability and customer satisfaction.
- Investing in preventive measures like training, process improvements, and quality management systems reduces failure costs and improves operational efficiency.
- Businesses can lower CoQ by enhancing process control, leveraging data analytics, and adopting proactive quality management strategies to optimize resource allocation and minimize waste.
The Cost of Quality (CoQ) represents the total investment a company makes to ensure products meet quality standards and the expenses incurred when quality failures occur. CoQ is divided into two primary categories: the cost of conformance, which includes prevention and appraisal costs, and the cost of non-conformance, which covers internal and external failure costs. Businesses that analyze and optimize their CoQ can improve product quality, increase customer satisfaction, and enhance profitability. Leading companies like Toyota and Dana Corporation have demonstrated that prioritizing quality initiatives reduces defects, lower employee turnover, and significant financial gains.
Understanding and controlling CoQ requires calculating and categorizing quality-related expenses. Prevention costs include quality training, supplier evaluations, and process improvements, while appraisal costs involve inspections, audits, and equipment calibration. Internal failure costs stem from production issues like scrap and rework, whereas external failure costs arise from warranty claims, recalls, and customer dissatisfaction. By strategically managing these costs, businesses can shift resources from reactive measures to proactive quality management, reducing inefficiencies and strengthening brand reputation.
Companies can minimize CoQ by investing in preventive strategies, improving process control, and leveraging data-driven insights. Implementing Six Sigma, Total Quality Management (TQM), and statistical process control (SPC) helps reduce defects and ensure process consistency. Automating inspections and using predictive maintenance further enhance quality control while reducing downtime and unnecessary costs. By focusing on quality from the design phase to post-production, organizations can create a culture of continuous improvement, boosting efficiency, profitability, and long-term market competitiveness.
Leave a Reply
You must be logged in to post a comment.