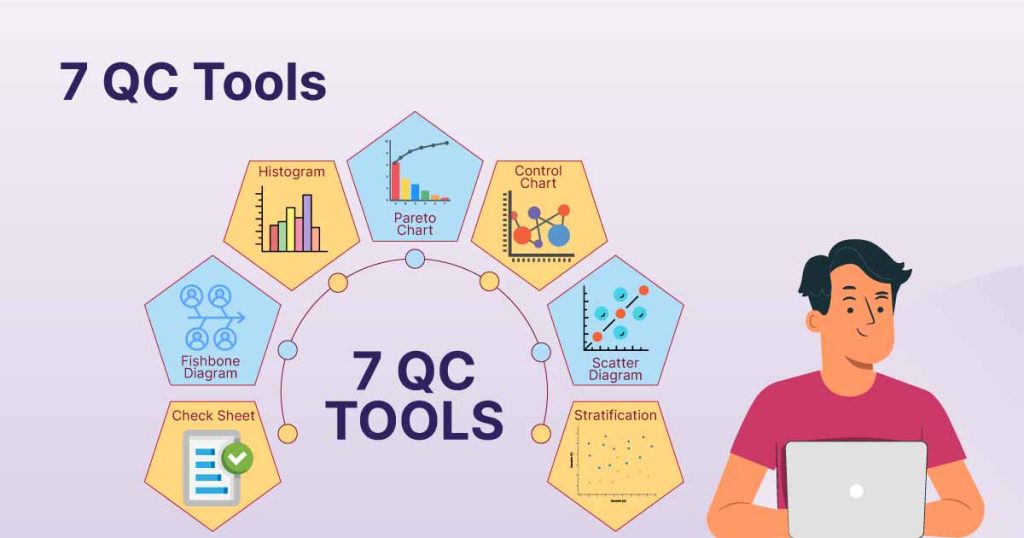
- The 7 QC tools are foundational problem-solving techniques for quality management, helping organizations identify and resolve quality-related issues.
- These tools improve processes, enhancing customer satisfaction through data analysis, root cause identification, and targeted solutions.
- Practical applications of each tool demonstrate how businesses can systematically address quality problems and continuously improve.
The 7 QC tools, developed by Kaoru Ishikawa, are essential for quality improvement and customer satisfaction across industries. These tools—histogram, Pareto Chart, Cause and Effect Diagram, Flowchart, Scatter Diagram, Control Chart, and Check Sheet—allow organizations to systematically analyze and resolve quality issues. Each tool helps businesses visually represent data, identify root causes, and implement corrective actions, leading to better decision-making and continuous improvement.
For instance, a restaurant chain using a histogram to analyze delivery times was able to streamline kitchen processes, resulting in faster service and improved customer satisfaction. Similarly, a manufacturing company used a Pareto chart to identify the top causes of defects, prioritizing their efforts on key issues that had the most significant impact. These examples highlight how the tools enhance quality and customer loyalty.
The tools are easy to use and require basic statistical knowledge, making them accessible to professionals at all levels. When applied effectively, these tools help businesses maintain consistent quality, solve recurring problems, and foster a culture of continuous improvement. As a result, organizations can meet customer expectations and build long-term trust.
Leave a Reply
You must be logged in to post a comment.