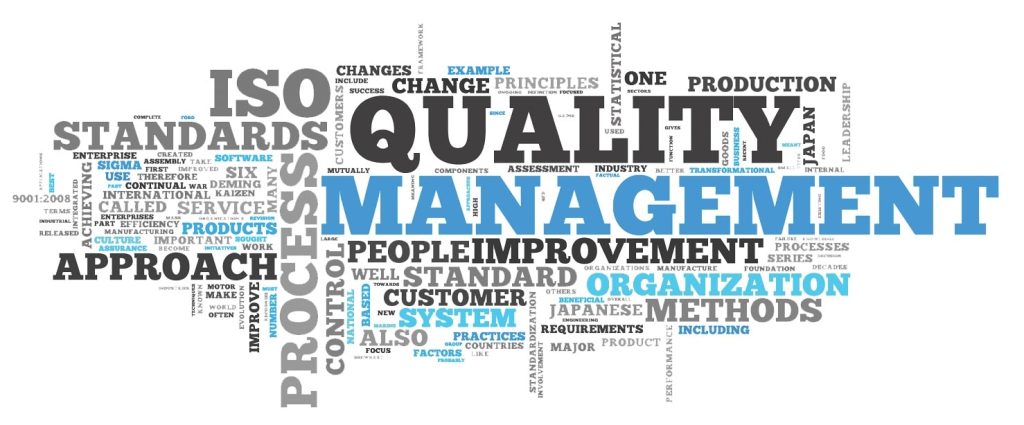
- Traditional compliance-based quality systems are reactive and siloed, failing to prevent rising product recalls or align with broader business goals
- Embedded Quality redefines quality management by aligning it with customer-defined outcomes, operational excellence, and integrated, value chain-wide strategies
- Organizations adopting Embedded Quality achieve major gains in throughput, profit margins, and customer value by leveraging automation, digital tools, and closed-loop processes
Conventional quality management, rooted in audits and regulatory compliance, is no longer sufficient to meet the demands of today’s competitive and volatile business environment. Chief Quality Officers (CQOs), now entering the C-suite, are expected to shift away from reactive, siloed practices and toward strategic leadership. Despite widespread compliance, product recalls have risen dramatically—up 50% since 2022—highlighting the failure of compliance alone to guarantee actual product quality. In many cases, quality teams remain disconnected from broader business goals, reducing their influence and impact across the organization.
To address these challenges is the concept of Embedded Quality—a transformative framework that integrates quality across the full value chain and centers it around “delivered quality,” or the value experienced by customers. Unlike traditional quality approaches that prioritize defect detection and regulation, Embedded Quality drives continuous improvement through proactive, digitally enabled processes. Key elements include predictive analytics, supplier collaboration, closed-loop systems, and the digital voice of the customer (DVoC), which translates end-user feedback into product and process improvements. The goal is to shift quality from a policing function to a strategic asset.
LNS Research’s benchmarking of over 300 industrial firms demonstrates the tangible benefits of Embedded Quality. Organizations identified as “leaders” in this approach enjoy nearly 30% higher throughput and 25% greater profit margins compared to those using traditional models. These companies embed quality into product design, supplier management, and manufacturing, achieving results that align quality with business outcomes. They also rely on emerging technologies like generative AI and enterprise quality management systems to reduce compliance costs and accelerate decision-making.
For CQOs looking to lead future-ready organizations, the Embedded Quality model offers a clear blueprint. Success depends on breaking down silos, aligning quality goals with financial metrics, adopting digital tools that automate and enhance compliance, and prioritizing customer experience as the guiding metric of quality. In this way, quality evolves from a reactive function into a business driver—ensuring not only compliance but long-term customer trust, operational excellence, and competitive advantage.
Read the full article (requires free ASQ log-in)
Leave a Reply
You must be logged in to post a comment.