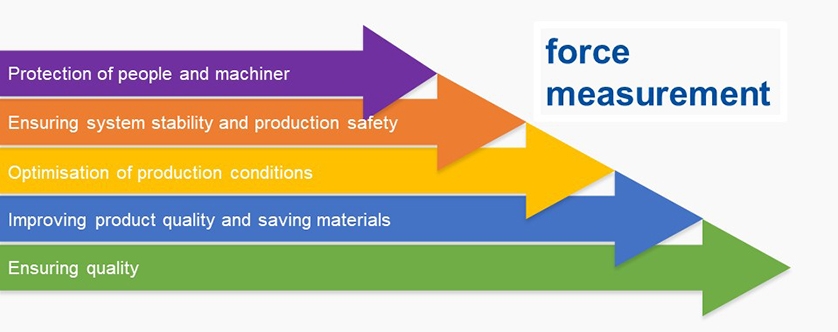
- Ensuring that products meet rigorous standards for quality and reliability is paramount, making force measurement a critical aspect of manufacturing.
- AI systems in force measurement employ complex algorithms capable of simulating human problem-solving and decision-making processes.
- The practical application of AI in force measurement involves preprocessing and cleaning data to ensure its quality before analysis. This is crucial as accurate data leads to reliable predictions.
Ensuring that products meet rigorous standards for quality and reliability is paramount, making force measurement a critical aspect of manufacturing. This testing method allows quality control professionals to verify that products are robust and comply with specified standards before they reach the market. Integrating Artificial Intelligence (AI) into this process has revolutionized how data from these measurements is analyzed, enhancing the ability to predict and prevent potential product and production failures before they occur. AI’s capability to efficiently process and analyze large volumes of data offers a significant advantage in identifying failure points and improving product quality.
AI systems in force measurement employ complex algorithms capable of simulating human problem-solving and decision-making processes. These systems utilize machine learning and deep learning techniques to analyze data collected from tests such as three-point bend tests or T-peel tests, which are essential for assessing the material properties of products. By applying AI to force measurement data, manufacturers can detect patterns and predict outcomes more accurately. This ability streamlines the quality control process and enhances the predictive maintenance of manufacturing equipment, potentially leading to substantial cost savings and increased operational efficiency.
The practical application of AI in force measurement involves preprocessing and cleaning data to ensure its quality before analysis. This is crucial as accurate data leads to reliable predictions. AI algorithms can adjust for “noise” in the data, such as mechanical vibrations, by using filtering techniques that maintain the integrity of the data trends. This cleaner, more reliable data can then be used to train AI models that predict when and how products might fail under various conditions. Ultimately, integrating AI into force measurement processes allows for more nuanced and forward-looking quality assurance strategies in manufacturing, making it an indispensable tool in pursuing excellence in product reliability and customer satisfaction.
Leave a Reply
You must be logged in to post a comment.