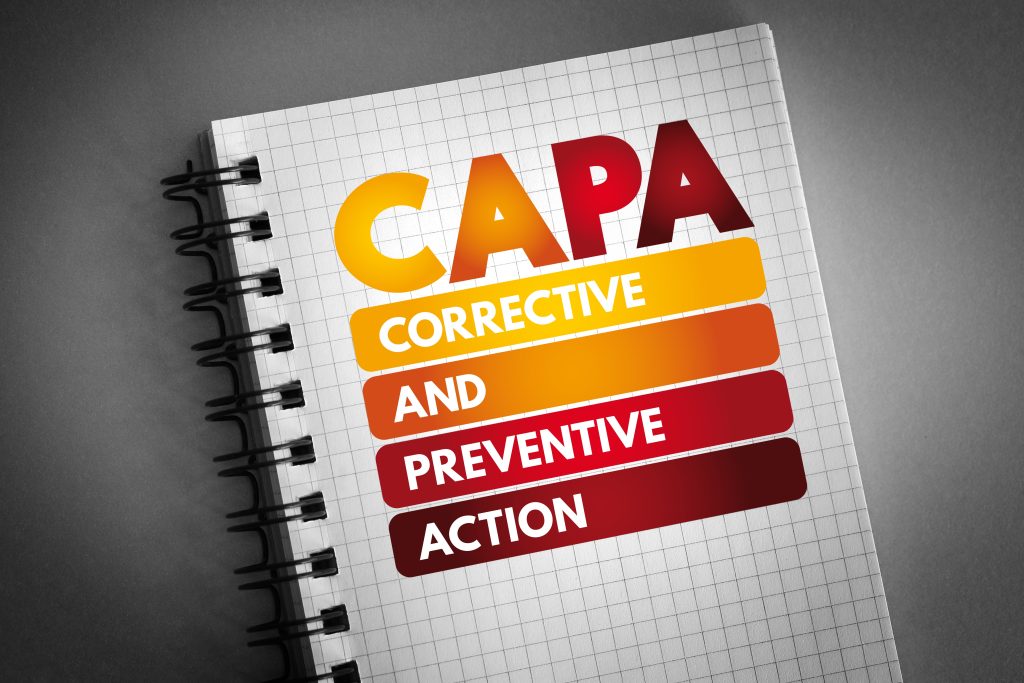
The article discusses the importance of a Corrective and Preventive Action (CAPA) system within a quality management system (QMS), particularly for organizations needing to comply with FDA regulations and ISO standards. A CAPA process is crucial for analyzing customer complaints and non-conformances to identify and implement corrective and preventive actions. Corrective action is a reactive measure taken in response to identified problems, while preventive action is proactive, aiming to prevent potential non-conformances.
The FDA’s Quality System Regulations mandate including a CAPA process in a QMS. These guidelines require analyzing processes, investigating non-conformances, implementing and verifying corrective and preventive measures, and documenting all actions taken. The key elements include addressing the causes of non-conformances, ensuring actions do not negatively affect product quality, and regularly reviewing the effectiveness of these actions.
The article also highlights familiar sources of CAPA events, such as customer complaints, audits, non-conformances in the manufacturing process, and procedure changes. However, not every event requires escalation into the CAPA system. Over-escalation can lead to an unnecessary backlog of CAPA processes (termed as being “CAPA happy”). At the same time, under-escalation can result in overlooked significant issues, potentially leading to warnings from the FDA.
Several factors should be considered to determine whether an event should trigger a CAPA: the frequency of the problem, availability of less resource-intensive alternatives, the issue’s relevance, past occurrences of similar issues, and verification of other actions taken to resolve the problem. Ensuring that decisions about initiating a CAPA process are made in collaboration with a dedicated CAPA administrator can help evaluate potential CAPA instances more effectively. This approach helps maintain the effectiveness of the CAPA system and the overall QMS.
Leave a Reply
You must be logged in to post a comment.