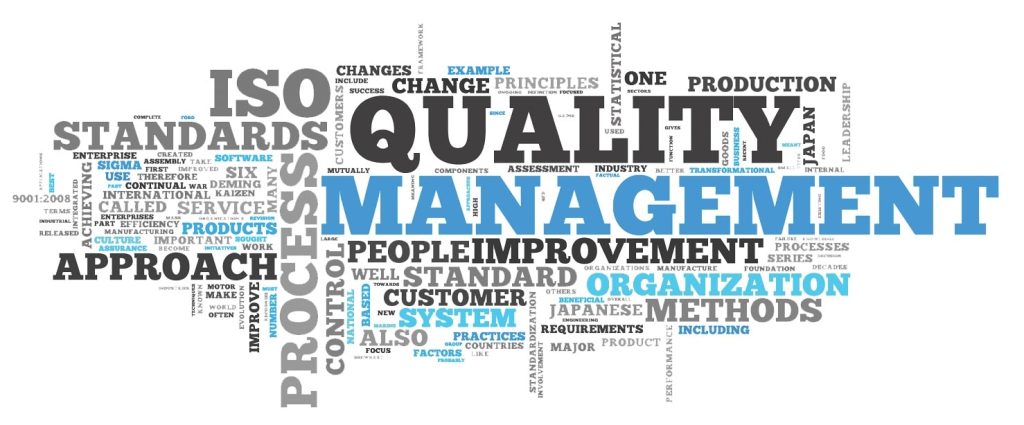
- Manufacturers are under increasing pressure in 2025 due to skilled labor shortages, supply chain disruptions, and the urgency to digitally transform operations.
- A strong quality management system (QMS) is essential for managing these risks, ensuring consistency, retaining institutional knowledge, and optimizing supply chain relationships.
- Digital transformation plays a crucial role in addressing inefficiencies by automating processes, improving data access, and enhancing predictive maintenance and supply chain visibility.
As manufacturers enter 2025, they face mounting challenges, including labor shortages, economic uncertainty, supply chain disruptions, and the pressing need for digital transformation. A recent survey of over 330 U.S. manufacturing leaders highlights these concerns, with 56% citing a lack of skilled labor as a top pressure driver and 45% identifying digital transformation as a priority. Additionally, companies fear the rapid loss of institutional knowledge and struggle to bring products to market quickly. Quality and senior managers express a gloomy outlook, with 84% expecting a recession within the next two years. These factors make a well-structured quality management system (QMS) more critical than ever for sustaining efficiency and competitiveness.
A QMS can directly address key pressure points by ensuring standardized work instructions, effective onboarding processes, and structured knowledge management. Best practices for work instructions include using clear language, visual aids, and maintaining consistency, while knowledge retention strategies involve aligning objectives with business goals, capturing both explicit and tacit knowledge, and leveraging technology for accessibility. The ability to navigate supply chain complexities is equally important, requiring companies to build strong supplier relationships, assess risks proactively, and diversify supplier bases to mitigate potential disruptions. Early warning signs such as deteriorating quality or changing payment terms can signal supply chain risks that need immediate attention.
Digital transformation is a key factor in helping manufacturers optimize operations and remain competitive. Companies must integrate automation, predictive maintenance, and real-time data analytics to improve decision-making and reduce inefficiencies. Connected systems facilitate seamless information flow, enhancing supply chain visibility and improving collaboration across teams. Many manufacturers struggle with internal data accessibility, which hinders productivity and increases pressure. By prioritizing areas that can have the most significant impact, companies can proactively make changes to improve their quality and efficiency, ensuring they are prepared for the evolving business landscape.
Leave a Reply
You must be logged in to post a comment.