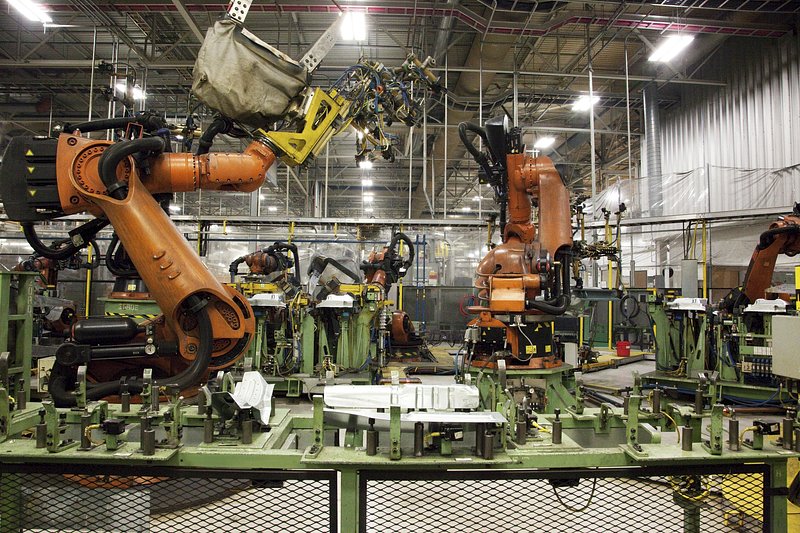
- Quality transmissibility describes how attributes from subassemblies impact the final product, making it crucial to understand effective quality control.
- Modeling quality relationships using data helps quantify the effect of subassemblies on final assembly, supporting problem-solving and continuous improvement.
- Complex interactions between subassemblies can create unforeseen quality issues, requiring advanced modeling and data-driven insights for resolution.
In manufacturing, every operation and subassembly contributes to the quality of the final product. Understanding how these attributes are transmitted throughout production is essential for identifying quality issues and implementing improvements. Quality transmissibility helps manufacturers analyze the relationship between individual subassemblies and the overall product, ensuring that even slight variations are accounted for in final quality assessments. By examining how quality attributes, such as dimensional accuracy, carry through assembly processes, companies can enhance their ability to detect and prevent defects before they reach the customer.
Modeling quality transmissibility enables manufacturers to establish quantitative relationships between subassembly attributes and final product quality. Linear models help determine how much a subassembly affects the final assembly, with a smaller slope indicating less impact. However, complex products often exhibit non-linear relationships, where multiple factors influence final quality. For example, both a car door and its frame may have minor variations that, when combined, create an unacceptable door gap. Understanding these interactions through data collection and statistical modeling allows for more precise quality control and root cause analysis.
Because subassembly interactions can amplify quality issues, manufacturers must consider unexpected variables such as residual stress or combined dimensional variations. By collecting real-world data and applying reflection modeling, organizations can gain deeper insights into quality transmission and optimize production processes. This approach not only helps resolve existing quality problems but also improves product design by identifying areas where subassemblies should be adjusted for minimal impact on final quality. Continued research into quality transmissibility will further refine these strategies, helping manufacturers achieve higher consistency and reliability in their products.
Leave a Reply
You must be logged in to post a comment.