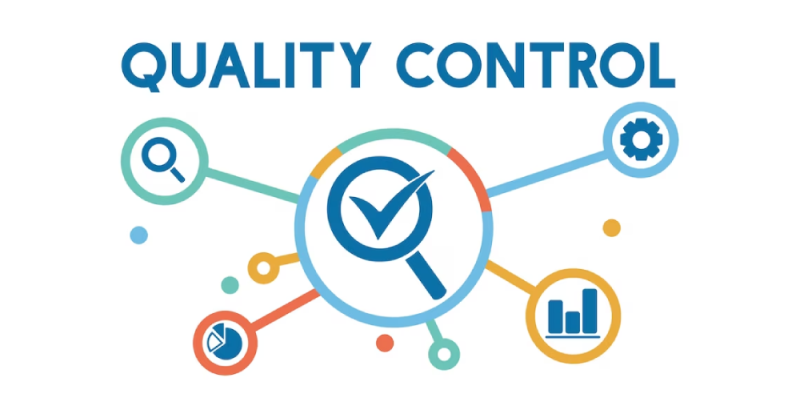
- Non-conformance refers to deviations from specified requirements in processes or products, categorized into minor and major non-conformances, with the latter posing significant risks to quality and compliance.
- Addressing non-conformance involves root cause identification, documentation, evaluation, corrective and preventive actions (CAPA), and proper segregation and disposition of non-conforming products.
- Preventing non-conformance requires strict adherence to standard operating procedures (SOPs), employee training, regular product testing, and consistent use of audit checklists to ensure compliance with ISO 9001 standards.
Non-conformance in the workplace occurs when processes or products fail to meet specified requirements, leading to inefficiencies, safety risks, or regulatory violations. It can be categorized into minor and significant non-conformances, with minor issues typically involving isolated documentation or procedural errors. In contrast, major non-conformances include critical failures such as shipping untested products, missing documentation, or unsafe working conditions. These deviations can have costly consequences, making organizations need to detect and address them effectively.
Managing non-conformance requires a structured process involving root cause identification, documentation, evaluation, and corrective actions. Following best practices such as adherence to SOPs, employee training, regular product testing, and audit checklists can help prevent these issues. The FDA and ISO 9001 guidelines recommend corrective and preventive actions (CAPA) for severe cases, ensuring that companies resolve non-conformances and implement long-term solutions to avoid recurrence.
A well-documented non-conformance process includes identifying the failure source, documenting the issue with relevant details, evaluating whether further investigation is required, segregating non-conforming products, and determining appropriate corrective actions. Digital tools can streamline this process by enabling organized reporting, real-time tracking, and automated analytics. Organizations can maintain quality standards, minimize disruptions, and improve overall operational efficiency by integrating a proactive approach to non-conformance management.
Leave a Reply
You must be logged in to post a comment.