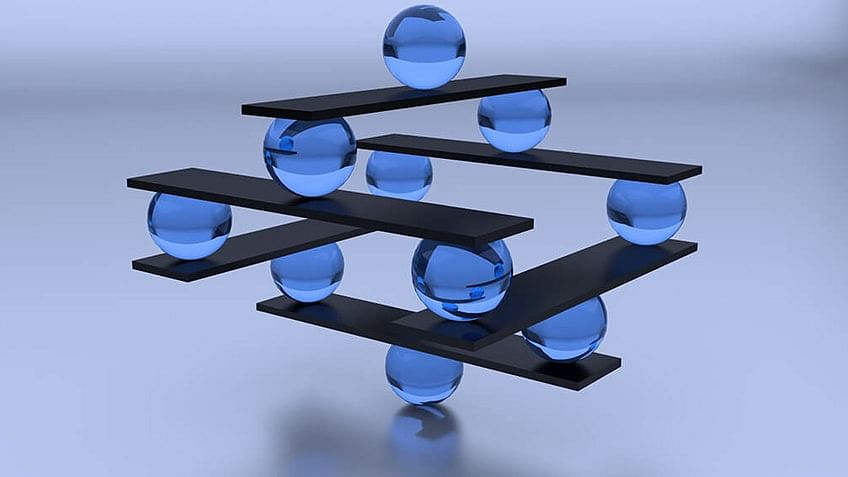
- Zero Defects is a quality management philosophy aimed at reducing waste and defects, emphasizing the principle of “doing it right the first time” while driving continuous improvement.
- Practical implementation of Zero Defects involves fostering a culture of quality, identifying and addressing potential defects, and integrating poka-yoke systems to prevent mistakes.
- While Zero Defects can boost customer satisfaction and reduce costs, its pursuit must balance realistic goals to avoid unnecessary strain on resources and employee morale.
The Zero Defects philosophy, introduced by Philip Crosby, advocates minimizing defects and waste to achieve high-quality standards in processes and products. Though it is often misconstrued as striving for literal perfection, Zero Defects is better understood as a mindset of continuous improvement and achieving acceptable quality standards under even stringent metrics. Six Sigma aligns closely with this philosophy, equating zero defects with 3.4 defects per million opportunities. Organizations adopting Zero Defects aim to instill a culture where quality is prioritized from the outset, minimizing the need for corrective measures later.
To implement Zero Defects, organizations need to establish clear quality standards, identify and mitigate potential sources of defects, and employ preventative measures such as quality audits and enhanced training. Strategies like poka-yoke systems—designed to prevent mistakes or make them easier to detect—help ensure robust processes. Continuous monitoring, data-driven quality assessments, and fostering an environment of proactive improvement further solidify this approach. Encouraging employee participation and rewarding quality achievements are key to embedding Zero Defects into corporate culture.
The benefits of Zero Defects include reduced waste, cost savings, and improved customer satisfaction, leading to greater customer loyalty and profitability. However, the pursuit of perfection can pose challenges. Unrealistic goals may strain resources, lower employee morale, and introduce inefficiencies, especially when full supply chain coordination is required. Striking a balance between ambitious quality standards and practical limitations is critical for sustainable implementation.
Ultimately, while achieving literal zero defects is unlikely, striving for the principles underlying this philosophy drives significant organizational improvements. By embedding the Zero Defects mindset into everyday practices, companies can enhance product quality, reduce costs, and foster a culture of continuous improvement that aligns with modern quality management standards.
Leave a Reply
You must be logged in to post a comment.