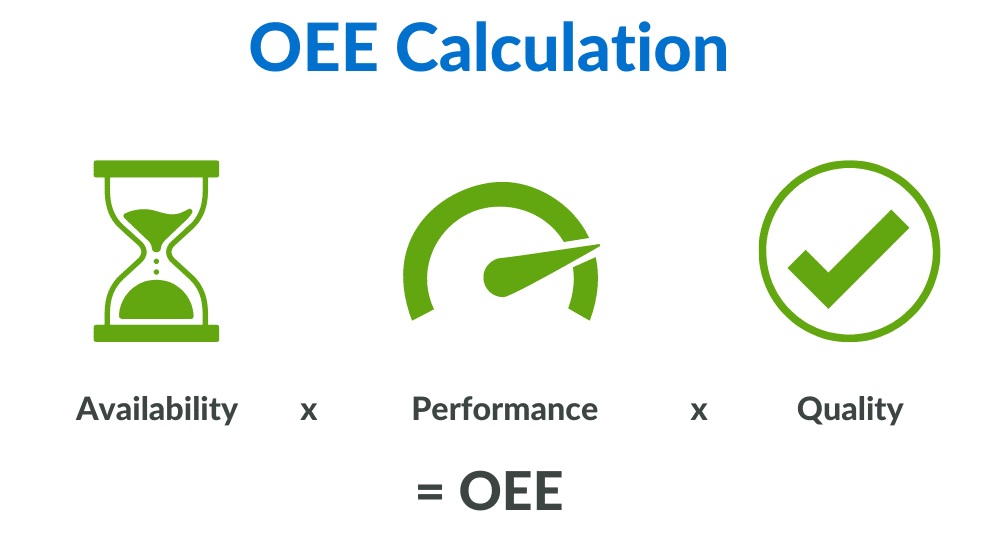
- Scrap and rework significantly increase quality costs and reduce Overall Equipment Effectiveness (OEE) by impacting availability, performance, and quality.
- By reducing scrap and rework, manufacturing companies can unlock substantial cost savings and boost productivity, efficiency, and customer satisfaction. These improvements enhance the bottom line and strengthen the company’s competitive position in the market.
- Plant floor audits, particularly those conducted with automated software, are pivotal in identifying and mitigating process errors. By enhancing quality performance and OEE, these audits are a key component of any quality improvement strategy.
Tracking quality metrics is crucial for continuous improvement, and understanding their interplay can help identify key leverage points for maximum impact. This article explores the relationship between scrap, rework, cost of quality, and Overall Equipment Effectiveness (OEE). OEE is a composite metric that measures availability, performance, and quality, where each element is negatively affected by the Six Big Losses, including equipment failure, minor stoppages, and defects such as scrap and rework.
Scrap and rework contribute significantly to quality costs. These costs are not just limited to wasted materials and time but also include hidden expenses such as waste disposal, detection and correction of defects, opportunity costs, reduced profit margins on reworked products, and lower production capacity. On average, scrap and rework can cost manufacturers up to 2.2% of their annual revenue, translating to substantial financial losses depending on the company’s size. For instance, a company with $100 million in revenue could lose $2.2 million annually due to these inefficiencies.
Reducing scrap and rework lowers the cost of quality and increases the number of conforming products, thereby improving OEE. Minor improvements in the quality rate can significantly enhance OEE. For example, increasing the quality rate from 83% to 93% can boost OEE from 59.9% to 67.2%, demonstrating the significant impact of reducing defects.
Plant floor audits are effective tools for identifying and correcting process errors that lead to defects. Regular audits can uncover issues like incorrect machine settings or non-adherence to standard work instructions. Automated plant floor audit software can streamline this process, reducing lag times, speeding up issue resolution, and providing better visibility into process nonconformance trends. By addressing these issues, manufacturers can significantly reduce scrap and rework, enhance quality performance, and improve OEE.
Leave a Reply
You must be logged in to post a comment.