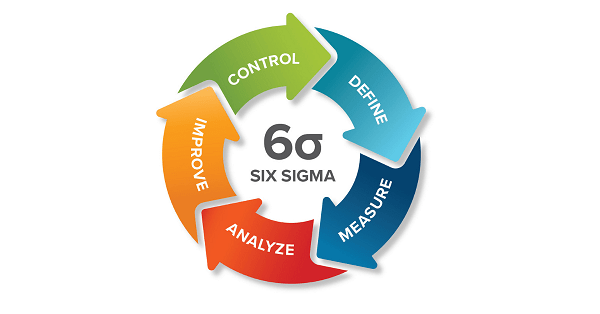
- Six Sigma Process Mapping is a visual tool for reducing errors and improving quality by detailing steps and relationships within a business process.
- The DMAIC framework—Define, Measure, Analyze, Improve, Control—is central to process mapping, providing a structured approach to identifying and addressing inefficiencies.
- Implementing best practices in process mapping, such as involving cross-functional teams and regular updates, significantly enhances operational efficiency and quality.
Six Sigma is a meticulous, data-oriented methodology designed to enhance business processes by minimizing errors and achieving nearly flawless operations. Process Mapping, a vital element of the Lean Six Sigma approach, provides a visual representation of a process, detailing the necessary steps and components to complete a task within an organization. Acting as a blueprint, it outlines the sequence of activities, the flow of materials or information, and interrelationships among process steps, helping organizations identify areas for improvement and streamline operations.
The DMAIC framework, comprising Define, Measure, Analyze, Improve, and Control, is central to Lean Six Sigma. Each phase of DMAIC plays a critical role in process optimization and, when combined with process mapping, offers a structured methodology for problem-solving and quality enhancement. Process maps illustrate current process flows, identify critical inputs and outputs, and uncover root causes of variations or defects. They facilitate the simulation of process changes and visualization of potential improvements, ultimately aiding in eliminating inefficiencies.
Various types of process maps serve different purposes within Six Sigma. Flowcharts document sequential steps and simplify complex processes, while SIPOC diagrams offer a high-level overview of Suppliers, Inputs, Processes, Outputs, and Customers, defining scope early in projects. Value Stream Mapping (VSM) analyzes material and information flow to identify inefficiencies, and Swimlane Diagrams organize steps by department, addressing communication and responsibility issues in multi-functional processes. Each type of map aids in understanding and improving specific process aspects.
Creating a Six Sigma process map involves several key steps: defining the process, gathering detailed data, involving the right team members, drafting and refining the process map, and distributing it to relevant stakeholders. Regular reviews and updates ensure the map remains accurate and useful. Avoiding common mistakes, such as overcomplicating the map or failing to involve a cross-functional team, is crucial for effective process mapping. By adhering to best practices, including keeping the process map simple, using process mapping software, and training team members, organizations can significantly enhance efficiency and quality, achieving operational excellence through targeted process improvements.
Leave a Reply
You must be logged in to post a comment.