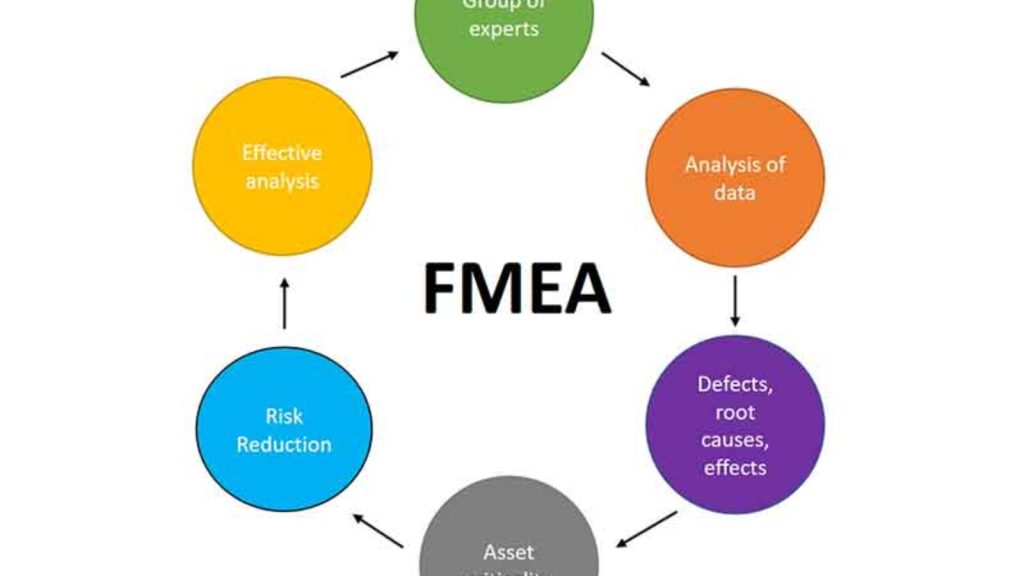
- The AIAG & VDA Failure Mode & Effects Analysis (FMEA) represents a significant shift in how Failure Modes and Effects Analysis is approached and applied in various industries.
- Implementing the AIAG & VDA FMEA methodology is essential due to the rapid technological advancements and associated risks in today’s products and services.
- Organizations are advised to conduct AIAG & VDA FMEA at several critical junctures: when introducing new designs or technologies, applying existing designs in new contexts, or making significant changes to existing designs or processes.
The AIAG & VDA Failure Mode & Effects Analysis (FMEA) represents a significant shift in how Failure Modes and Effects Analysis is approached and applied in various industries. Originally rooted in the automotive sector, FMEA methodologies have broadened to include industries like aviation and medical equipment, highlighting its universal relevance. The AIAG & VDA FMEA, a collaborative effort between AIAG and Germany’s VDA, introduces a revised manual designed to unify and standardize FMEA practices globally. This new methodology emphasizes prevention over detection and introduces a structured seven-step process, replacing the traditional Risk Priority Number (RPN) with an Action Priority (AP) system to better prioritize risk mitigation actions.
Implementing the AIAG & VDA FMEA methodology is essential due to the rapid technological advancements and associated risks in today’s products and services. It offers a robust framework that enhances the ability to analyze and mitigate risks comprehensively. This unified approach not only simplifies the understanding of FMEA requirements globally but also enhances the focus on preventive measures, thereby improving product safety and reliability across various manufacturing and service sectors.
Organizations are advised to conduct AIAG & VDA FMEA at several critical junctures: when introducing new designs or technologies, applying existing designs in new contexts, or making significant changes to existing designs or processes. The process involves a detailed examination of potential failures to improve products proactively before market release. Ultimately, this methodology fosters a more efficient, effective, and standardized approach to risk management, supporting organizations in achieving higher safety and satisfaction benchmarks in their product and service offerings.
Leave a Reply
You must be logged in to post a comment.