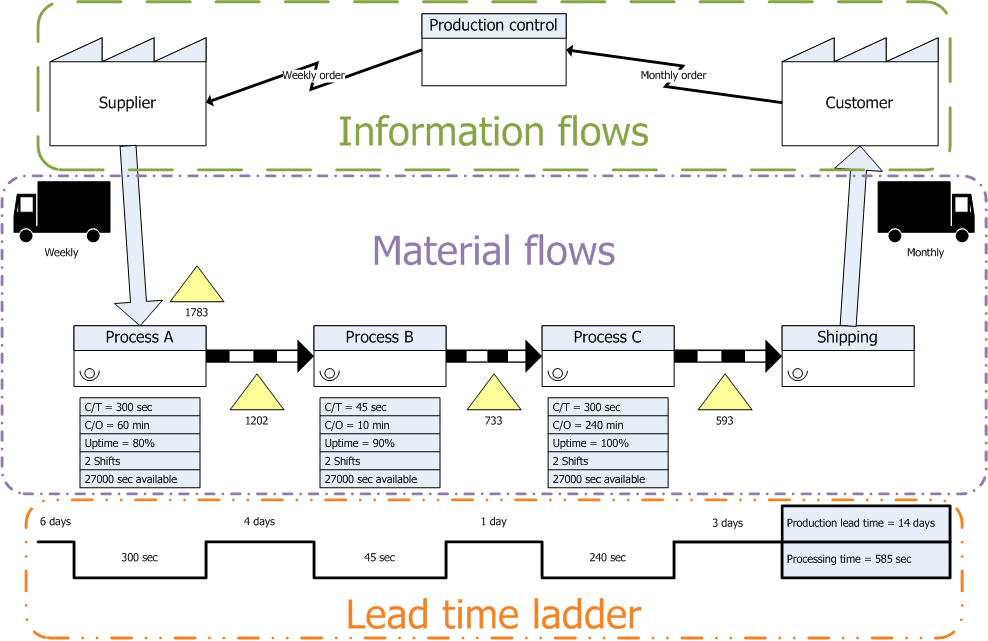
- Value Stream Mapping (VSM) is a pivotal tool in Six Sigma, a methodology that aims to improve product quality and efficiency by minimizing errors, variations, and waste.
- VSM incorporates detailed analyses of each step in a workflow, integrating Six Sigma’s focus on waste reduction through the DMAIC (Define, Measure, Analyze, Improve, Control) framework.
- As part of a comprehensive Six Sigma strategy, VSM supports waste reduction and fosters a collaborative culture focused on continuous improvement. This ensures that operational processes align closely with organizational goals and customer expectations.
Value Stream Mapping (VSM) is a pivotal tool in Six Sigma, a methodology aimed at improving product quality and efficiency by minimizing errors, variations, and waste. Initially developed in manufacturing environments such as Motorola and later adapted across various industries, including finance and healthcare, VSM is a visual method that analyzes and optimizes the entire flow from raw material to delivered product. It involves detailing every required action to transform raw materials into finished products, helping organizations identify inefficiencies and non-value-added activities. By creating a visual map, stakeholders can view all components involved in the delivery process, facilitating a more efficient and lean approach to process improvement.
VSM incorporates detailed analyses of each step in a workflow, integrating Six Sigma’s focus on waste reduction through the DMAIC (Define, Measure, Analyze, Improve, Control) framework. It identifies and helps eliminate waste, ensuring every step adds value to the customer. Moreover, VSM is about identifying current inefficiencies, planning, and transitioning to a more optimized future state. This tool uses symbols and components, such as process boxes, customer and supplier icons, and flow indications, to map out and scrutinize every activity within the process landscape.
The historical roots of VSM trace back to the early 20th century innovations by Henry Ford, later refined by Taiichi Ohno of Toyota, integrating flexibility and variety into production processes. Today, VSM is applied across diverse sectors, proving particularly effective in settings like healthcare, where it can dramatically enhance patient flow and service delivery. Moreover, advanced VSM integrates digital tools for real-time data analysis, improving the accuracy and efficacy of process improvements. As part of a comprehensive Six Sigma strategy, VSM supports waste reduction and fosters a collaborative culture focused on continuous improvement, ensuring that operational processes align closely with organizational goals and customer expectations.
Leave a Reply
You must be logged in to post a comment.