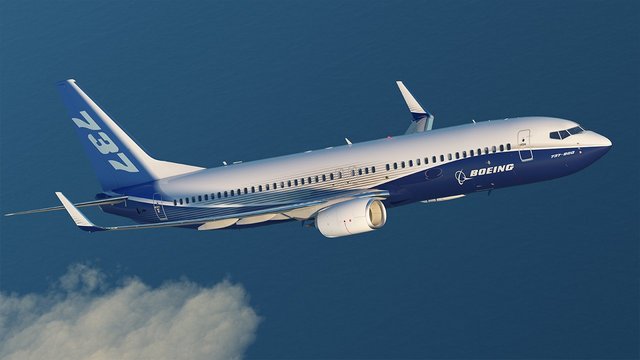
- Boeing has faced significant scrutiny over its manufacturing practices, which have recently been linked to several quality and reliability issues.
- Key factors contributing to these incidents include accepting substandard parts from suppliers, deferred problem-solving to later stages in the production process (termed “traveled work”), and intense pressure on workers to expedite production to meet deadlines.
- To mitigate such risks, best practices in manufacturing emphasize the importance of addressing problems at their initial detection. This involves implementing effective quality control processes that empower workers to take ownership of their work and resolve issues before moving to the next stage.
Boeing has faced significant scrutiny over its manufacturing practices, which have recently been linked to several quality and reliability issues, including the high-profile 737 Max series air crashes and a near-disaster involving an Alaska Airlines Max 9. Key factors contributing to these incidents include accepting substandard parts from suppliers, deferred problem-solving to later stages in the production process (termed “traveled work”), and intense pressure on workers to expedite production to meet deadlines. This environment prioritized financial outcomes over stringent quality control and safety, leading to recurring failures and risks. Boeing’s troubles are not as isolated as they may seem, and other companies can (and should) use Boeing’s challenges as an opportunity to evaluate their own quality practices.
For example, “Travelled work,” a term that describes not addressing issues immediately when detected, has been particularly problematic for Boeing. This approach has led to critical oversights, such as the door plug incident with the Alaska Airlines plane, where missing bolts were not rectified promptly, resulting in significant safety risks. This practice indicates a deeper systemic issue within Boeing’s production culture, where known problems in parts and assemblies are not resolved at the point of identification but are passed along the production line, often leading to oversight and failure.
To mitigate such risks, best practices in manufacturing emphasize the importance of addressing problems at their initial detection. This involves implementing effective quality control processes that empower workers to take ownership of their work and resolve issues before moving to the next stage. Proper training of suppliers and rigorous inspection of incoming components are crucial to maintaining high standards. Additionally, fostering a culture where quality and safety are prioritized above speed and cost efficiency is essential. Boeing’s recent adjustments, such as rejecting inadequate fuselages and sending them back for rework, reflect a shift towards these best practices. However, consistent application and cultural change are necessary to prevent future failures.
Overall, Boeing’s experiences underline the critical importance of integrating robust quality management systems and maintaining rigorous standards throughout production. By learning from these incidents, manufacturers can better understand how to structure their operations to avoid similar pitfalls, ensuring that quality and reliability are upheld to prevent costly and dangerous outcomes.
Leave a Reply
You must be logged in to post a comment.