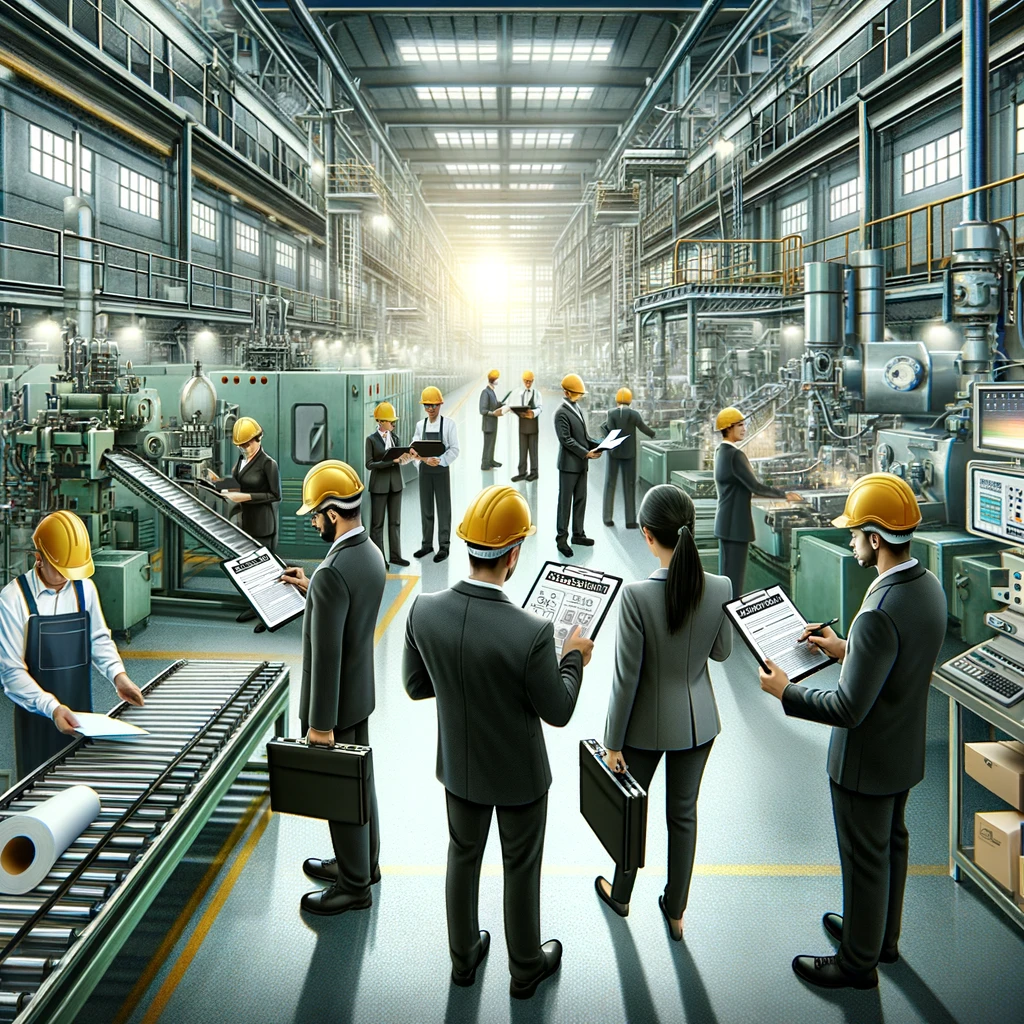
- The article outlines a structured approach to help decide which factory audit is appropriate, considering disruptions caused by the coronavirus pandemic and other political tensions that may restrict physical access to the factory.
- The willingness of a supplier to undergo an audit may be influenced by the size of the potential order or the demand for their product.
- For ongoing supplier relationships, especially with key suppliers, setting up an annual auditing program is advisable to monitor changes in the supplier’s business practices and systems over time.
Choosing the right factory audit is crucial for importers to evaluate potential suppliers’ reliability, capabilities, and risks. Given the variety of factory audits available, making the right selection depends on several factors, including the possibility of conducting an on-site audit, the supplier’s willingness to be audited, and the specific aspects the buyer wishes to check. The article outlines a structured approach to help decide which factory audit is appropriate, considering disruptions caused by the coronavirus pandemic and other political tensions that may restrict physical access to the factory. In such cases, an ‘E-audit’ is recommended, where the supplier’s standard operating procedures and records are reviewed remotely, including through video calls with production supervisors. This method offers a fast, cost-effective alternative to traditional on-site audits.
The willingness of a supplier to undergo an audit may be influenced by the size of the potential order or the demand for their product. If a supplier hesitates, suggesting a less formal “factory visit” conducted by a professional auditor might be a viable alternative. This approach allows for some level of on-site evaluation without the full structure of a traditional audit. Once an audit is accepted, buyers must decide what areas to focus on, such as the quality system, social compliance, readiness to take orders, or other concerns like environmental impact or supply chain security. The type of audit selected could range from a Quality System Audit (QSA), which checks the manufacturer’s quality management systems, to more specific audits focusing on social compliance or environmental impact.
For ongoing supplier relationships, especially with key suppliers, setting up an annual auditing program is advisable to monitor changes in the supplier’s business practices and systems over time. This can help push for continuous improvement and maintain a high quality and compliance standard. The article further elaborates on different types of audits, including Initial Factory Evaluation (IFE), Quality System Audit (QSA), Blended Systems Audit (BSA), Social Compliance Audit (SCA), Process Management Audit (PMA), and Layered Process Audit (LPA), each tailored to meet different auditing needs based on the user’s specific requirements and concerns. This comprehensive approach to selecting and conducting factory audits can significantly aid buyers in making informed decisions about potential suppliers, ensuring product quality and compliance with relevant standards.
Leave a Reply
You must be logged in to post a comment.