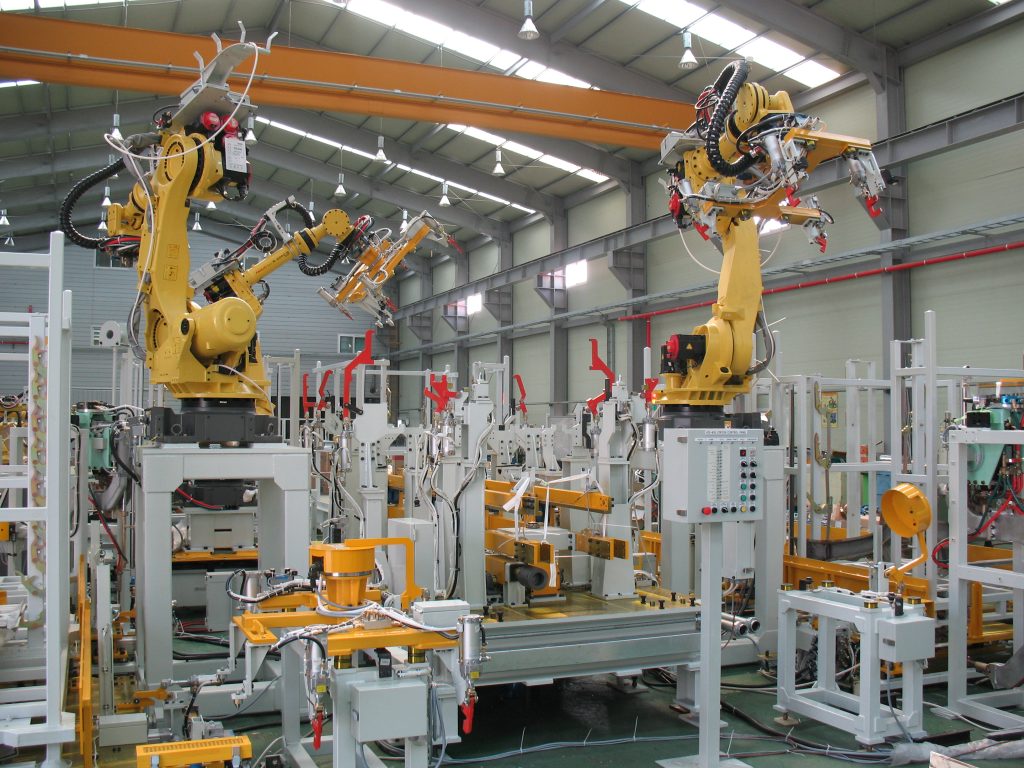
This article explores the impact of connected worker software in reducing manufacturing costs. The article begins by noting the significant costs associated with poor quality in manufacturing, as reported by the American Society for Quality (ASQ). These costs can range from 10% to 40% of revenue, translating to substantial losses for large manufacturers. The article argues that connected worker software solves these challenges by improving several key areas of manufacturing operations.
First, the software enhances the consistency of plant floor checks. Traditional methods like manual Excel and paper checklists are labor-intensive and often lead to low audit completion rates, impacting product quality and production costs. Connected worker software allows quick access to digital checklists on mobile devices, enabling real-time identification and correction of process errors. This approach has been shown to reduce downtime, minimize defects and complaints, and decrease scrap and rework costs. A case study of Valeo, an automotive wiper manufacturer, demonstrates how the software led to a 50% reduction in quality costs by addressing a specific defect efficiently.
Another significant advantage of connected worker software is connecting workers to real-time assistance. Traditional manufacturing setups often leave front-line workers isolated, making it challenging to address issues promptly. The software enables real-time communication and collaboration among plant workers and other departments, which can reduce defects and downtime. For example, it allows workers to quickly request resources or consult experts via video chat, minimizing the need for onsite specialist visits.
Centralizing frontline knowledge is another key benefit of connected worker software. By digitally organizing crucial process information such as standard operating procedures (SOPs), safety guidelines, and troubleshooting guides in one place, the software streamlines production and prevents costly errors. It also facilitates customized knowledge delivery, online troubleshooting, workforce development, and timely reminders, reducing process errors and improving production efficiency.
Additionally, leveraging Internet of Things (IoT) sensor data on the plant floor is a growing trend in manufacturing. The software is a critical link connecting IoT data with plant floor operations, aiding in better anomaly detection and equipment optimization. For instance, in an automotive assembly process, the software can guide operators to quickly identify and address equipment issues, like faulty sensors, thereby reducing production slowdowns.
Finally, the article discusses how connected worker software accelerates issue management. It enables capturing detailed data, assigning and tracking action items, ensuring accountability, documenting solutions, and verifying corrections. This integrated approach has helped manufacturers significantly reduce overdue corrective actions and internal defects, lowering scrap costs.
Leave a Reply
You must be logged in to post a comment.