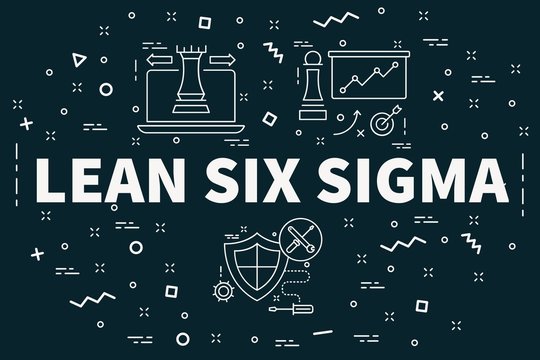
This academic study published in “The TQM Journal,” addresses the gap between financial measurement and Lean Six Sigma (LSS) methodologies in process improvement initiatives. The study aims to enhance employee engagement by designing a process and a benefit measuring methodology that aligns with financial metrics and LSS principles, particularly in eliminating waste.
The research identifies a common problem in many businesses: the lack of a defined process or knowledge for costing LSS project improvement actions. This gap often leads to misunderstandings and a lack of engagement among employees as they struggle to understand the financial implications of process improvements. To develop a cost-benefit analysis model, the study uses the Design for Lean Six Sigma (DFLSS) and DMADV (Define, Measure, Analyze, Design, Validate) methodologies. This model helps employees align financial costs with non-value waste costs and poor quality costs.
In the Define phase, the researchers established a problem statement and project charter through focus group discussions. They used a SIPOC (Suppliers, Inputs, Process, Outputs, Customers) diagram to identify the critical components of the process and recognize the lack of a straightforward costing process. During the Measure phase, surveys assessed employees’ understanding of productivity and cost measurement. In the Analyze phase, workshops with finance, project leaders, and management were conducted to understand the challenges and brainstorm solutions.
The Design phase led to the creation of a guideline or roadmap as a process map, which helps employees identify and categorize tangible benefits of process improvements. This roadmap is supported by a reference document generated by finance, providing necessary data for benefit calculations. The validation phase involved training project leaders, managers, and employees in the new methodology, with subsequent surveys showing significant improvements in understanding and confidence in benefit calculations.
The study’s findings demonstrate that a precise, understandable method for calculating the benefits of Lean Six Sigma projects can significantly increase employee engagement and the success of process improvement initiatives. The research emphasizes the importance of aligning LSS concepts with financial data and providing employees with the tools and knowledge to quantify the benefits of their improvement ideas. The methodology developed in this study can benefit any company facing similar challenges in integrating LSS and financial measurements.
Leave a Reply
You must be logged in to post a comment.