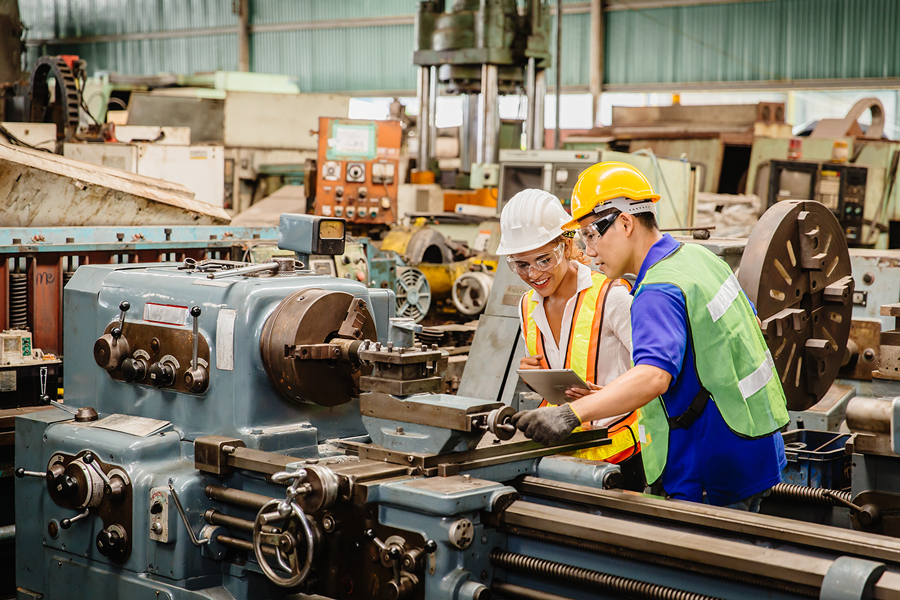
- Choosing the right type and timing of quality inspections depends on product risk, supplier experience, and how critical defects are to your business
- For repeat production by experienced factories, final random inspections may suffice; for first-time production or higher-risk items, earlier and more thorough inspections are needed
- A risk-based, flexible approach can reduce costs, maintain quality, and strengthen supplier relationships without over-investing in unnecessary oversight
This podcast episode from Quality Inspection includes a discussion outlining a decision-making framework for selecting quality inspections based on production context, using a flowchart developed from nearly two decades of industry experience. Inspections are essential for verifying product quality at key stages—especially when working with external or upstream suppliers. If a factory is experienced and producing a known product, the risk is lower, and a final random inspection may be sufficient. However, assumptions about supplier capabilities must be carefully verified, as even reputable factories may subcontract or alter materials without notice.
When a product is being made for the first time, or by an unfamiliar supplier, earlier inspection points such as pre-production meetings, first article inspections, or in-line inspections are critical. These allow for early detection of errors and allow factories to correct issues before full-scale production continues. The nature of the product also matters—low-cost, low-risk items may tolerate higher defect rates, while high-value or sensitive products (like electronics or jewelry) require stricter inspection routines, possibly including 100% inspections before shipping.
Additional inspection strategies include off-site inspections, often used by Japanese companies, where products are checked by a third party before being shipped abroad. This method adds control, especially in cases where the cost or risk of receiving defective goods is high. Inspections can also be combined with labeling, kitting, or bundling tasks, especially when keeping sensitive information away from suppliers.
Long-term, companies should refine their inspection strategies based on supplier performance. Consistently high-performing factories may allow for reduced inspection frequency or skip-lot inspections, keeping pressure on suppliers without unnecessary spending. A sound inspection plan, grounded in a clear understanding of production risks, product importance, and supplier reliability, helps organizations strike the right balance between cost and quality assurance.
Leave a Reply
You must be logged in to post a comment.